From planning permission to choosing construction and roofing methods, here’s what to think about before you get started connecting an extension to your home.
Thinking about adding an extension to your house? Whether it’s a new kitchen, living space or simply more room to breathe, knowing how to properly connect an extension to your existing home is just as important as the design itself.
Do I need planning permission?
The good news is that in many cases, the answer is no—thanks to something called permitted development rights. These rights allow you to extend your home without applying for full planning permission These rights vary slightly across the UK:
England
- Single-storey rear extensions: Up to 4 metres for detached houses.
- Height restrictions: Maximum height of 4 metres; eaves height no more than 3 metres if within 2 metres of a boundary.
- Coverage: Extensions must not cover more than 50 per cent of the land around the original house.
Wales
- Single-storey rear extensions: Must not extend beyond the rear wall of the house by more than 4 metres and cannot exceed 4 metres in height.
- Height restrictions: If within 2 metres of a boundary, the eaves height cannot exceed 3 metres.
- Materials: Should match the existing house as closely as possible.
Scotland
- Single-storey rear extensions: Permitted development allows extensions up to 4 metres in height.
- Coverage: The extension must not project more than 3 metres from the rear wall of the original house and must not be within 1 metre of a boundary.
Northern Ireland
- Single-storey rear extensions: Should not extend beyond the rear wall of the original house by more than 4 metres for detached houses.
- Height restrictions: Maximum height of 4 metres; eaves height no more than 3 metres if within 2 metres of a boundary.
Of course, it’s always worth checking with your local council. Rules can vary depending on whether your home is listed, located in a conservation area, or has already been extended before.
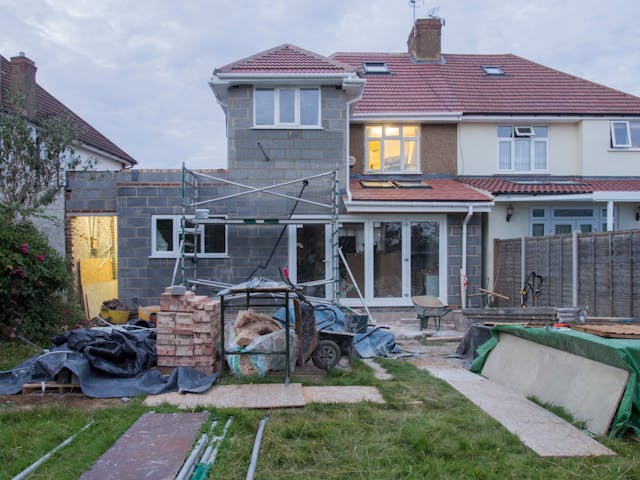
Methods of construction
Before deciding how to build your extension, ask yourself: do you have the time and expertise to manage the project, or even do some of the work yourself? Taking that route means hiring different trades for various stages, from laying foundations to final finishes. It’s not a decision to be taken lightly. Most people opt to hire a builder to handle the entire job. Either way, you’ll need professional drawings – for planning permission if required, and definitely for Building Control.
[adrotate banner="58"]The method of construction is an early and important decision. Traditional options include brick and block or block and block with an insulated cavity. But with rising insulation standards and greater focus on energy efficiency, alternative systems are becoming more attractive – and more widely available, even for extensions.
Timber frame
One such method is timber frame, where the structure is supported by timber panels. It’s a precisely engineered system, making for a strong and quick build. The external finish can vary – brick or block, stone, render, tiles or weatherboarding. Exposed timber frames, usually in oak, are popular for their visual appeal, often combined with structural insulated panels (SIPs) to fill the gaps between beams. This method works well for large glazed areas and can be used for both walls and roofs.
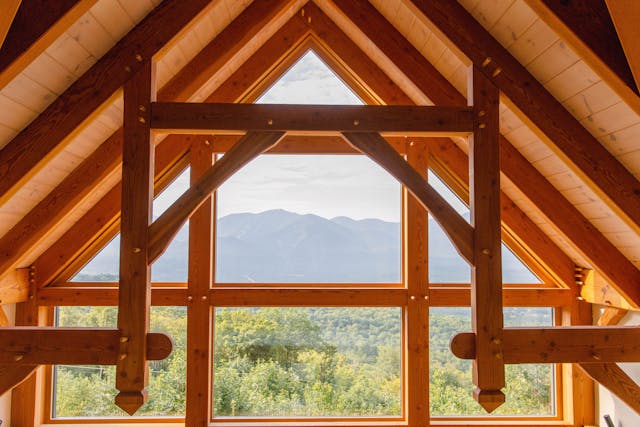
SIPs (structural insulated panels)
SIPs are a development of timber frame construction. These sandwich panels have a core of dense insulation between layers of oriented strand board (OSB), offering both structural support and high thermal performance. Made in a factory, they generate little waste, are quick to erect and significantly reduce air leakage.
Advantages: Fast and efficient build, reduced waste, minimal reliance on wet trades and excellent energy performance.
Disadvantages: Long design and engineering lead times, limited pool of experienced contractors and site access is key. SIPs tend to cost more upfront but save money through quicker builds and energy savings.
Steel frame
Prefabricated steel frames are rarely used for domestic extensions unless large internal spans are needed. Their strength makes them suitable for open-plan layouts but they are more commonly found in commercial projects.
Insulated concrete formwork (ICF)
ICF uses hollow polystyrene blocks that interlock like Lego and are then filled with concrete. These provide excellent insulation, both thermal and acoustic. Internal finishes can be plastered, while external cladding is similar to that used on timber frame buildings.
Advantages: Quick to build, outstanding insulation, no internal supporting walls required and easy to create curves.
Disadvantages: Typically more expensive than timber frame, although this varies with concrete prices. Future changes (e.g. new openings) require cutting into solid concrete. Services must be pre-planned. Skilled operatives are essential.
Glass
Bringing more light into the home is often a key reason for extending, which makes glazing a priority. Glass box extensions have become increasingly popular, offering a dramatic architectural feature.

Eco friendly alternatives
Sustainable options like hempcrete and straw bale offer breathable walls with strong thermal mass. These natural materials help regulate indoor temperatures year-round and contribute to a healthier internal environment. However, they are not structural and require a supporting frame, usually timber. Exterior finishes are typically clay or lime-based plasters. As non-standard methods, they require specialist builders or training courses.
Methods of roofing
Your new extension’s roof will need to connect to the existing structure. The design might be flat, single-pitched, or double-pitched, depending on your home and its surroundings.
Flat roofs
Modern flat roofs are cost-effective and far superior to those of the past. The most common system is a single-ply membrane, usually around 2mm thick, made from thermo-plastic or thermo-set materials. Laid in sheets and sealed at joints, this creates a continuous waterproof layer with a lifespan of up to 40 years.
Thermo-Plastic Membranes: uPVC is widely used and reinforced with fibreglass or polyester. Seams are heat or chemically welded and as strong as the membrane itself.
Advantages: Lightweight, quick to install, resistant to chemicals and recyclable.
Disadvantages: Requires high-quality installation. A poor seam or puncture compromises waterproofing.
Thermo-Set Membranes: Rubber-based, such as EPDM. These are sealed with adhesive or tape to create watertight seams.
Advantages: Excellent weather resistance, fast installation, good value.Disadvantages: Vulnerable to puncture, and proper sealing is crucial.
Green roofs
Green roofs are increasingly popular. Extensive versions use lightweight sedum blankets suitable for timber decks, while intensive roofs, designed for gardens, need a concrete structure. Both provide thermal and sound insulation.
The roofing system must include waterproofing, drainage and a growing medium. The vegetation shields the roof, extending its lifespan to up to 50 years.
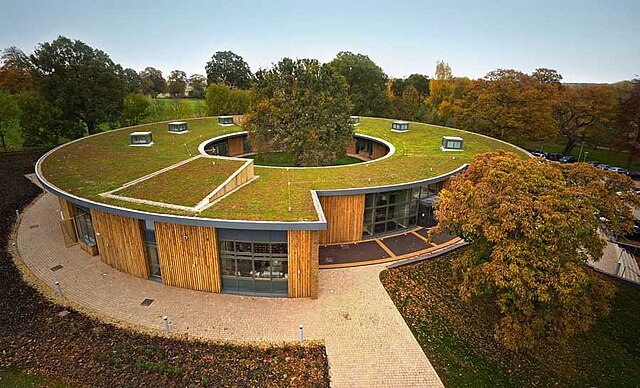
Pitched roofs
A pitched roof could be a lean-to (single pitch) or a gabled (double pitch) style. The pitch must be steep enough for slate, tile or shingle finishes – usually a minimum of 22 degrees. A pitched roof can match the existing house or create contrast through material or colour.
Beneath the roof covering are layers of felt or breather membrane, insulation and a damp-proof membrane. Interior finishes may include plasterboard or cladding. If there is an open roof void, it will need ventilation, and insulation must meet or exceed Building Control standards.
Connecting an extension what to consider
Connecting a new extension to an existing house requires thoughtful detailing. Walls must be properly tied together to avoid future structural issues. A vertical damp-proof course may be necessary between the old and new walls. If your existing wall is cavity-built, this must continue into the extension to maintain insulation and prevent cold bridging.
Where cavities are uninsulated, adding insulation is advisable. Traditionally, builders connected new and old walls using a technique called toothing – cutting into the existing wall to interlock bricks or blocks. This creates a strong, seamless join but is labour-intensive and must be precisely executed to match materials and align bonds.
7 Comments