Ryan Daly chats about why he chose timber frame as the build method for his home in Co Down and shares what the experience was like.
In this article we cover:
- Why he chose timber frame
- How much it cost
- What the timber frame company provided
- What it was like from delivery to putting up the kit
- Troubleshooting on site
- Heating and cooling systems
- EPC/SAP with house/plot sizes
- Floor plans and supplier list
Why did you choose timber frame as the method of construction?
I have worked in the low energy housing sector as a renewable energy engineer for the last 16 years. I’ve seen a lot of selfbuilds in that time and the best performing houses in terms of comfort and low running costs were those built with timber frame.
Plot size: 1 acre
House size: 310sqm
Bedrooms: 5
Heating and hot water: geothermal heat pump with PV
Ventilation: centralised mechanical ventilation with heat recovery
Build method: timber frame
EPC (SAP): A (97)
I’m delighted we went down that route. The design process was straightforward – because our site already had outline planning permission, we just had to do a reserved matters application which took six months to come through. We had our architect John design our house and we were delighted with him and his team in what they came up for us. We gave them a two page brief on things that we wanted and this ensured they came up with the design we wanted straight off. We just went back with a few minor tweaks. After this the timber frame company took the drawings and came up with their own structural and timber frame drawings.
There were no amendments needed to the plans. Our house has four different levels on the ground floor but overall I think it was easier to build the house in timber frame than what it would have been in block.
How did you choose which company to go for?
We’ve worked with the timber frame supplier we chose for a number of years now, and I was fortunate to see the various stages of their builds. I got to witness their approach first hand and I was super impressed. When you walk in and see the level of insulation, the airtightness membrane and tapes, plus the thermal bridging detailing, it made so much sense to choose this route.
The positive feedback from their previous customers plus the fact that I realised while the same approach to airtightness and thermal bridging can be taken in masonry builds, a lot of the success of this comes down to a contractor who has knowledge in applying these
measures, which is often sadly lacking. Also there are a lot more straight lines and even surfaces in timber frame houses which always helps with installation.
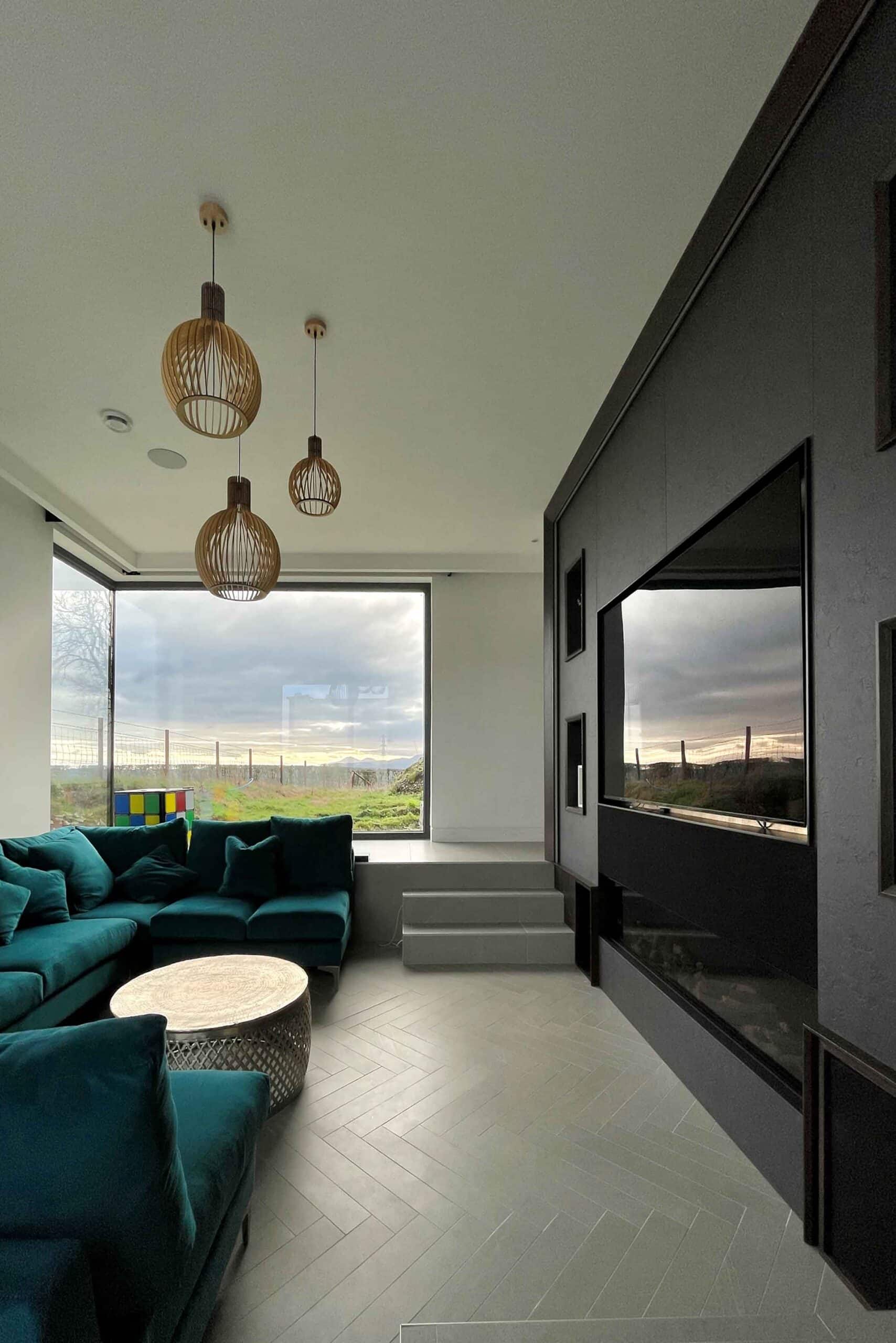
What did the timber frame company provide?
The timber frame kit, associated steel frame to support the timber structure, and the windows. They also provided a complete airtight solution through the tapes and membranes that they use and this element for us is the key to ensuring we have a low energy house.
We liked the idea of getting the window and timber frame package all from the one company as I realised after doing some research on windows that the preparation work was as important as the actual window install.
The timber frame company was excellent in providing the technical details prior to the window installation and worked with us on site to ensure this was all 100 per cent before they came to install them. Even though we went direct labour, we found the timber frame team very obliging and we got great advice from them on other matters of our build, which we really appreciated.
What was it like on site, from delivery of the kit to putting it up?
It was great to see it coming on a lorry one day and being erected the next. The kit arriving had to be one of the most exciting parts of doing our selfbuild. It all came together rather quickly. We waited six weeks to get the roofing contractor to come which was in January 2021. A lot of moisture had got into the timber at that stage but the timber frame company reassured us that with their system, it was able to make its way out with their intelligent airtightness membrane, which was reassuring.
Any hiccups on site and how were they dealt with?
When the timber frame company was on site installing the windows on the first day my phone rang at 10am and I thought oh here we go!
I was waiting for them to say the openings for the windows were incorrect or they had mishandled a window and smashed it. In fact, one of the installers had to move a bit of scaffolding to get a window in and accidentally dropped a length of it close to our garage roof and smashed the glass on one of our solar panels.
Our timber frame supplier kindly offered to compensate us to supply and fit a new panel. It felt like we were in safe hands; I was very relaxed about things. When doing a self-build not everything is going to go right; it is a case of trying to make as few mistakes as possible and having the right people there to ensure that.
How much did the timber frame cost?
Just under £100K and our steelwork was around £30k. Our running cost for the first year in the house for all our heating, hot water and cooling was just £132.
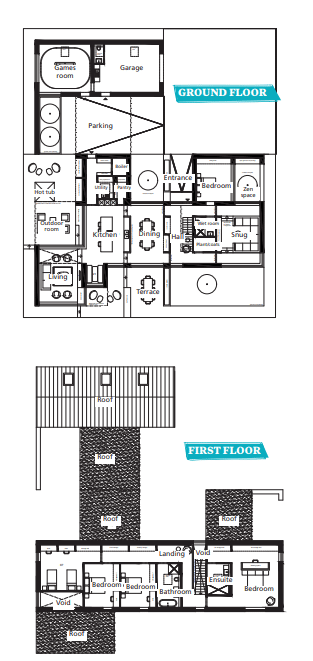
What heating and cooling system did you get?
Timber frame houses perform exceptionally well in the winter but there is a concern about overheating in the summer as they are so well insulated and airtight. We got around this by installing a ground source heat pump (GSHP) which can provide passive (free) and active cooling in the summer.
This was one of the best things we did. Our cooling system ran for the hot summer months of 2022. It means our house is a comfortable temperature all year round and as the GSHP is powered by our solar photovoltaic (PV) system, it costs pennies to run it.
Suppliers
Architect: BGA Architects, bga-ni.com
Timber frame company: Kudos, buildingkudos.com
SAP calculation: Elmhurst Energy