Ronnie and Denise Slater’s oak frame home was their fourth and final to build; this is how they did it on a site with views of Belfast Lough.
In this article we cover:
- Drawing on their previous self-builds for experience
- Oak frame build choice
- Pros and cons of oak frame building
- Foundations and what it was like on site
- Choice of gas boiler with underfloor heating
- Choice of solar thermal panels
- Ventilation system
- Kitchen design details
- Landscaping details
- Top tips and pitfalls to avoid
- How they stayed on budget until second fix and how they went over
- Professional photographs and specification
When you’ve put down roots and raised a family it’s very hard to leave after 40 years, especially if you built the house yourself. But life moves on, the house is now too big and not ideal for retirement living, it’s time to think about where to go next. Ronnie and Denise Slater’s situation is one that will strike an answering chord with many couples, as will their solution.
Inspired by the many TV programmes and magazines now available on self-build, Ronnie and Denise began the search for a site for their fourth self-build, within a five mile radius of their present home and with similar views across Belfast Lough.
Recounting to a friend one day the tale of yet another disappointing site search, the visitor looked out of the window at the large garden and asked ‘why don’t you build there?’ “Once he’d suggested it” Ronnie told me as we looked out over the blue summer sea, “it seemed obvious. Perhaps it was because to us it had a label saying ‘garden’, not ‘site’.”
If planning permission could be achieved, the problem would be solved. The Slaters were clear that what they wanted to build was a well insulated house requiring little heating. Timber frame they felt was the most likely to achieve this, but the designs they saw from the companies they approached in England failed to inspire them.
The same cannot be said of green oak frame, but there was a concern that this type would be expensive and complicated to build. “In fact it was extremely quick” Ronnie continued, “and following an overnight stay in their show house in England we knew we had found what we were looking for.”
Mention the word ‘Planning’ to any self-builder, and it usually results in groans and expressions of frustration. Happily, this was not Ronnie and Denise’ experience. “Before starting on the design, we met with a very helpful lady from the planning office who finished by wishing us a successful outcome. Next was a visit to site by the English designer whose suggestions were modified by both parties until, six months later, we were ready to press the ‘Start’ button” said Ronnie.
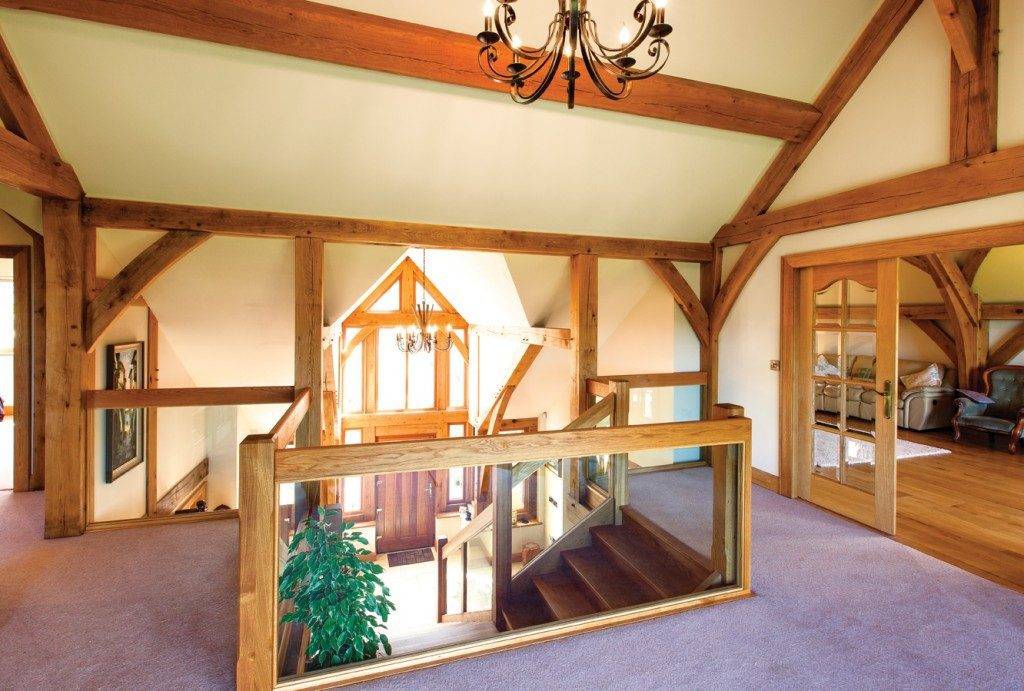
The design the company produced was based on a written brief from the Slaters, but because oak frames do not like cold, wet climates as the oak will expand and contract in response to the weather, and it is thus difficult to keep the buildings watertight, the oak really comes into its own in the interior.
The internal layout only required some minor tweaks as the interpretation of Ronnie and Denise’s ideas was very accurate; the company were also very helpful in ensuring a smooth journey through planning.
Building is a messy and noisy business and living as they do with neighbours on either side, the Slaters visited them and explained what would be happening. It all got underway in November, with the oak frame booked to arrive at the end of the month, but rain very nearly stopped play because, as Ronnie vividly recalls, the heavy clay soil had become liquid mud.
Digging foundation trenches was impossible until the whole area was stabilised with five lorry loads of stones. The tolerance of a timber frame is only 10mm +/- so it is essential that the foundations are absolutely accurate. The oak frame duly arrived and in the space of four days, the Slater’s had the skeleton of a house. Although it is a very solid, massive structure, the beams and braces are held together with oak pegs, as designed by the company’s structural engineers.
The next stage was the addition of the pre-fabricated stud panels, which unfortunately coincided with one of the coldest winters on record. Despite temperatures down to -12deg C, heavy snow and strong winds, the joiners appeared every morning at 7.20am and kept the build on track. By January the cladding of the frame and roof were complete, making the house watertight and ready for the external brick and tile finishes.
In their previous build, Ronnie had used a concrete roof tile, but found that the sand washed out of it over time. Since then, manufacturing technology has greatly improved and it is now possible to get a concrete tile that looks like clay, but is much less expensive, and it has a 15 year guarantee.
The tiles are cambered in two directions and give an attractive ‘textured’ effect. At the suggestion of their roofing contractor, the vertical gable end was also hung in these and the result is a perfect balance between the vertical wall and sloped roof.
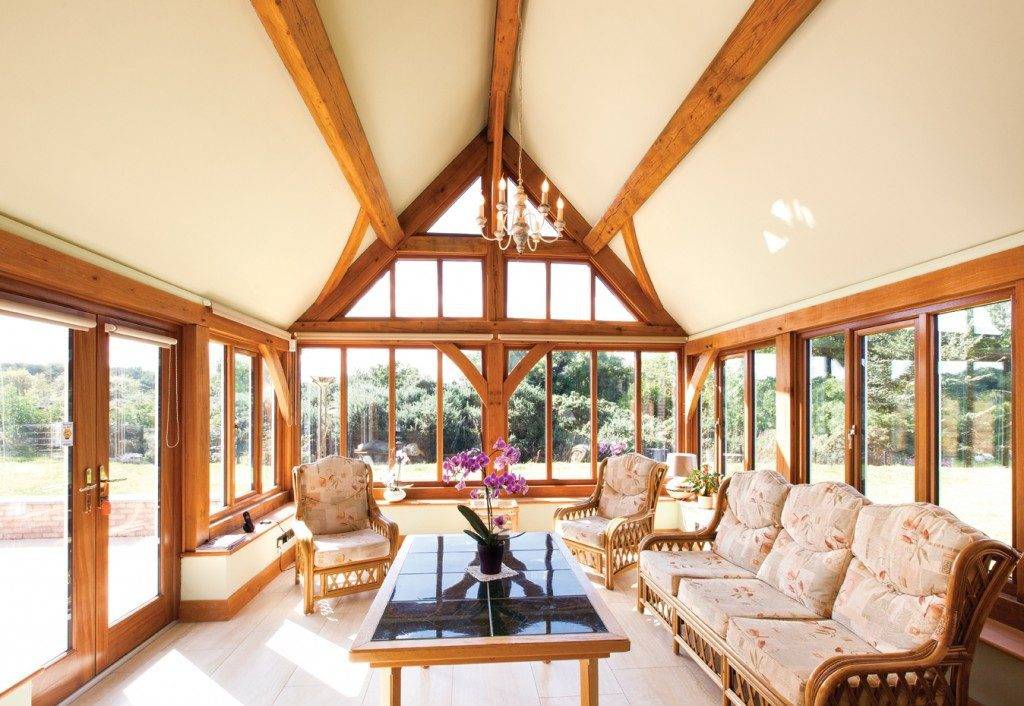
Inside, the Slaters chose underfloor heating downstairs as the floor covering is mostly ceramic tiles, except for the snug and dining area which are in oak. Upstairs there are radiators, but because the house is so well insulated and benefits from solar gain, the open area hall allows the warmth to travel throughout the house and these have yet to be used.
The heat source is a condensing gas boiler fed from the mains, but this was not the original intention. With an eye to the future and wishing to keep energy bills to a minimum, Ronnie investigated the possibility of a ground source heat pump, but came to the conclusion that it would not be a wise investment for them.
“I found that the articles I read and the information we were given from distributors conflicted widely. I read a thesis by an MSc student at Strathclyde University which said that in their experiments, the best COP (coefficient of performance, which is the ratio of heat delivered, to energy input to the compressor or pump), never exceeded 3.3, very different from the figures of between 4.5 and 5 we were being given. The article also demonstrated that heavy, wet clay is particularly unsuitable for a ground source heat pump, and that decided the issue.”
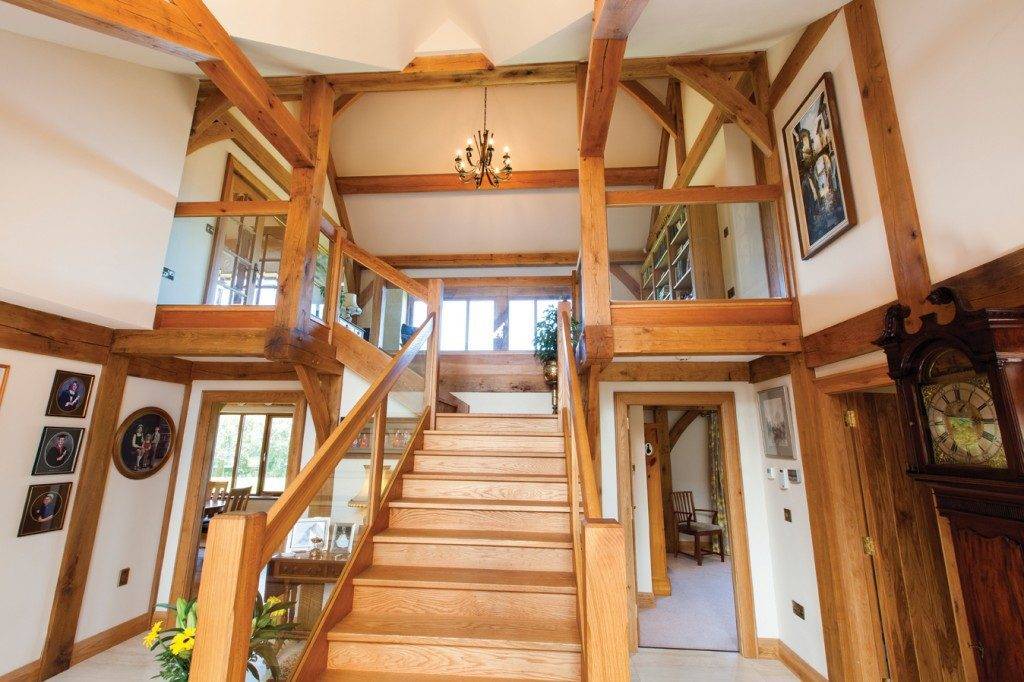
The Slaters do have evacuated solar tubes on the roof which give an average 55 – 60deg.C pre heat to the water, even in this poor summer when there’s been so little sun and it’s also been cold. The gas boiler then brings the cylinder up to temperature when needed.
Sound attenuation is an increasingly important aspect of building and one which Ronnie and Denise took into consideration with their house. A masonry build has advantages in that the block partition walls are better at absorbing sound than timber frame studs, which in the Slater’s house are filled with mineral wool, whilst the upstairs floors have a 1cm thick acoustic underlay underneath the carpet.
“As a sailing man, I remember a boat we had where the engine was housed in a layering of rubber, lead and then more rubber, and despite its being diesel, standing next to it you could speak normally. Although what we have in our internal walls and on the floors upstairs has reduced the transfer of sounds, I think this is an area where it’s worthwhile doing as much as you can.”
Lighting is another area which is sometimes not given the attention to detail it should, and this was something Ronnie felt could either make or mar the oak frame. He is unstinting in his praise of the electrician who, as he put it “thought laterally” for both inside and out. The result is a house where the lighting is accurate, attractive and yet unobtrusive where it needs to be. That is just one of the changes the Slater’s have noticed, 40 years on from their first build when lighting a room consisted of a pendant in the centre of the ceiling.
Also receiving close attention to its design was the seating at the breakfast bar in the kitchen, this time by Ronnie. He ensured that the granite worktop, table surface and the bar stool are all in correct relation to each other so that you can keep one foot on the ground and the other on the bar of the stool. A very neat solution to an awkward corner where two wall units meet at right angles is a shelf system that means pots and pans are easily accessible without having to get down on the floor.
An instant supply of hot water and the induction hob that cools instantly have both been a great success, although the latter resulted in a new set of cookware, as Denise explained. “It works by magnetism so we took a magnet with us to the shops and tested all the pots and pans to make sure they would work before we bought them.
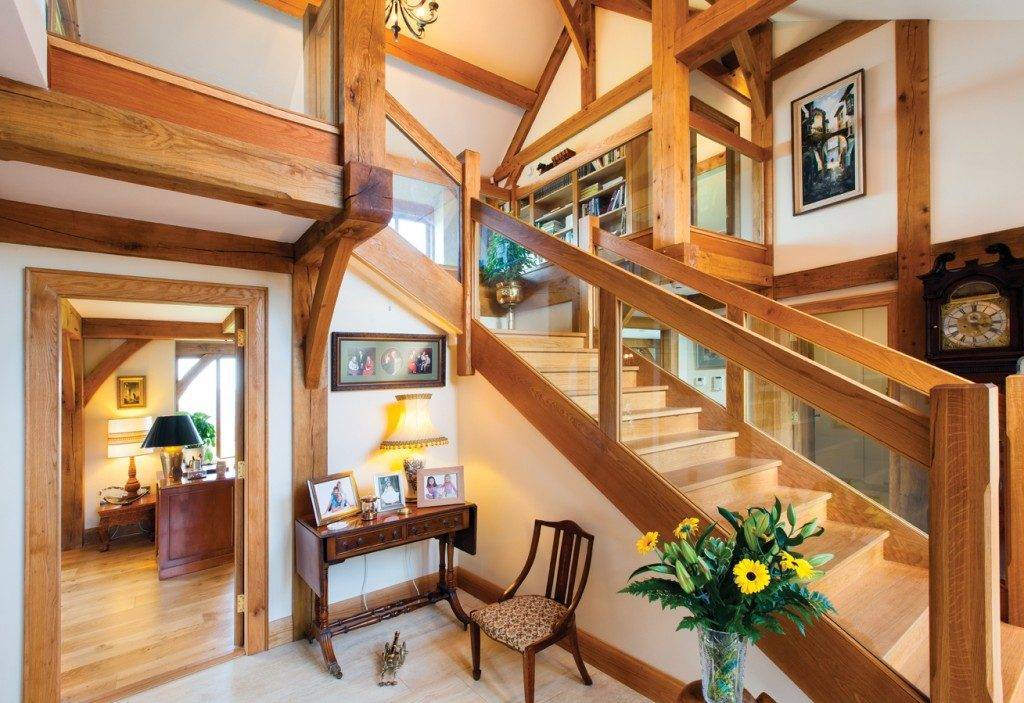
The ‘cool’ room we’ve had to re-think slightly because although we don’t have underfloor heating, the freezer there made it the warmest.” As in the Building Regulations, an airtight test was carried out when the house was virtually completed, with the requirement being to achieve a reading of below 10m3/hmsq. The house passed with flying colours, scoring 2.28m3/hmsq. To obtain a score as low as this requires great attention to detail to ensure the vapour membrane is not perforated – to the extent of there not being even a letter box allowed.
Ventilation is mechanically controlled with heat recovery. Every build is unique and so there are bound to be teething problems. Although celebrating his 80th birthday during the build, Ronnie is very modern in thought and included a whole house sound system.
Unfortunately there were prolonged difficulties which have happily now been resolved, allowing them to play, for a small monthly charge, a vast range of music in any or all of the rooms.
The Slaters also experienced difficulties with their carbon monoxide detectors when they discovered, quite by chance, that these would not activate in smoke. This was rectified by the installation of a new system.

Having put so much effort into the detailing of the build, many self-builders have run out of energy and ideas, (not to mention money), when it comes to landscaping. Ronnie and Denise had a very simple, and effective, solution. Theirs is a marine environment and the soil is cold and heavy so initially they did the easiest thing and created a large area of lawn. A particularly good tip for anyone in a difficult environment like this is to look around and see what is flourishing in other people’s gardens, Ronnie advises.
In time, the various shrub beds will be planted with species similar to those in their previous garden. Although retired and keen to take an active part in the build, Ronnie felt that professional help in the form of a project manager to oversee everything would give them peace of mind. Unfortunately ill health resulted in the person appointed having to resign early on, but by this time Ronnie felt he knew what was involved and took on the role himself. This experience left him with some words of advice for others contemplating a self-build.
“I asked my secretary to come out of retirement and her work was vital to the whole operation. At the end of every week the accounts were right up to date and I knew, to the penny, how much had been spent. I found that very comforting. Preparing the VAT claim is an arduous chore but financially very important, and having everything accurately recorded on spread sheets made the process, not easy, but certainly easier.”
Ronnie’s second suggestion is to employ a good Quantity Surveyor who knows the building trade inside out. He will look after your interests and make sure you get value for money. On a practical level, he will help to find tradesmen, compile tenders, assess replies, draw up contracts and give advice if you are concerned over any aspect of the build.
A third suggestion, which may not always be possible, is to see everyone on site every day. The Slater’s were very fortunate in that they sold their existing house before starting to build, but thanks to the generosity of the new owner, were able to go on living in it during the year of the build. Without this help the new house project would not have been possible.
Ronnie was therefore on hand to open the site every day and a knock on the door was all that was required for an instant site meeting. Ronnie’s final thought is on the subject of payment. “Sometimes it’s hard to tell if everything has been done correctly until later in the process. For this reason it’s a good idea, if you can, not to pay fully for it all until it’s been tested, which generally happens when you move in.”
He is also very clear about the importance of everyone pulling together on the building of their new home. “I’m not a construction professional and don’t have all the answers, but when we explained what we wanted to achieve, everyone drew on their experience and as a result we got this lovely house! At the end of it all we’d a great party for everyone involved, as well as their wives and even babies, it was a wonderful way to start our new life here.”
“The project was on budget until second fix, but from that point it started to go considerably over. There were several reasons for this. Firstly, some contracts were allowed to go ahead on an hourly basis, rather than a fixed price. Secondly, some ‘luxury’ items were chosen which could not be fitted at a later date, such as the sound system, motorised gates and garage doors. Thirdly, and most importantly, there were no compromises in the name of economy.”
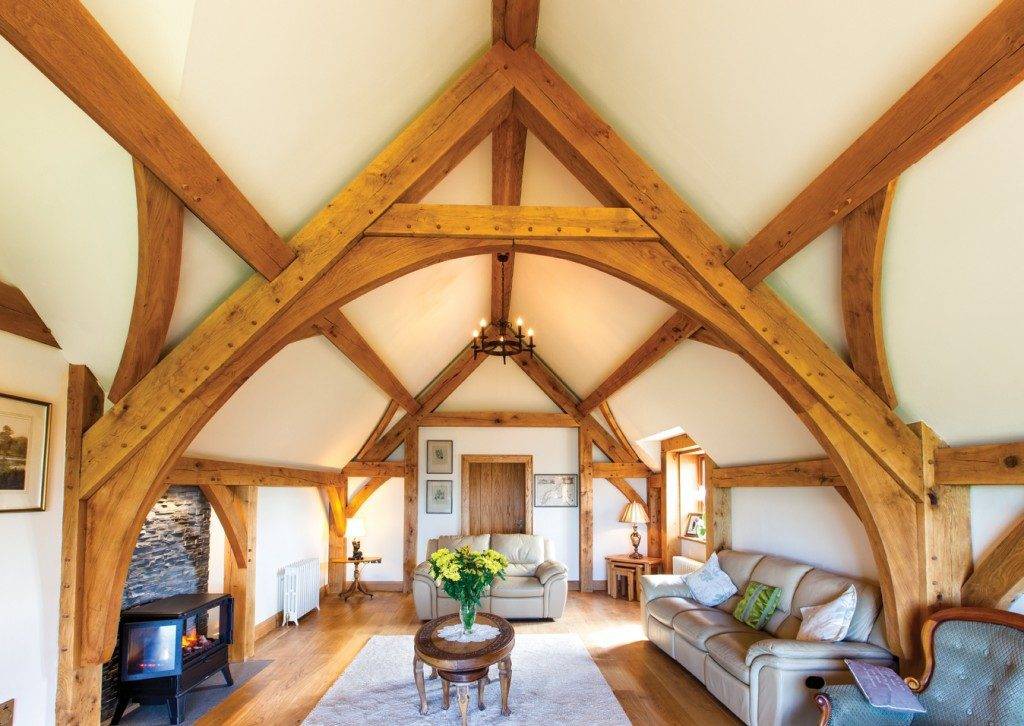
Spec
House size: Main house 310sqm, garage with space above 105sqm.
Site size: 3/4 acre
Walls: facing brick/50mm cavity/membrane faced o.s.b/140mm stud filled with mineral wool insulation/Intello vpm/50mm service duct filled with mineral wool/37.5mm insulated plasterboard comprising 25mm rigid insulation bonded to 12.5mm plasterboard. Overall 396mm thick. U value 0.15W/msqK
Floor: 225mm foil backed rigid insulation below 50mm self levelling screed. U value 0.09
Roof: ventilated cavity below tiles/Solitex vpm /125mm rigid foil backed insulation/Intello vpm/50mm counter battens/37.5mm insulated plasterboard. U value 0.15W/msqK.
Windows: triple glazed (Krypton) Iroko wood with powder coated marine grade aluminium exterior, varnished wood interior. U value 1.1W/msqK