What is timber frame, structural considerations, environmental considerations and how to design around the eco friendly building method.
In this article we cover:
- What is timber frame
- Are there design limitations with timber frame
- Is timber frame the best solution for your design
- How a timber frame building goes up
- Structural considerations
- Environmental credentials of timber frame
Building your walls out of timber frame is, in most cases, environmentally friendly, provides flexibility in design, and quick to put up on site.
In the world of self-building, timber frame most often refers to the method of building walls from wood. At its most basic, lengths of timber and sheathing are assembled to make structural wall panels. In Ireland, the term timber frame most commonly refers to factory made timber frame panels or kits, often sometimes pre insulated, that are then craned into place on site.
Timber frame design considerations
In theory, as long as it complies with the relevant standards and regulations, there are no limits to the design possibilities of creating a timber frame home. Even curved walls are possible with some clever detailing.
The main limitation is span but, thanks to the addition of steel or engineered timber, can easily be dealt with. This relates to large open plan spaces and clear spans of floors, roofs and walls.
Further limitations set by the various regulations affecting the design and construction of timber frame residential buildings apply to such things as the height of each storey and overall height of the building, fire safety, workmanship, selection of materials, etc.
For the design stage, you would just need to verify whether timber frame construction is in fact the best solution, and indeed the most cost effective, for the house that you want. In general, timber frame construction costs are equivalent to bricks and mortar for a near zero energy building specification.
But don’t despair if your original design was intended for a traditional bricks and mortar construction, as it can be adjusted to suit a timber frame structure. If you have already obtained full planning permission, the type of structure shouldn’t matter as long as the external appearance remains as approved.
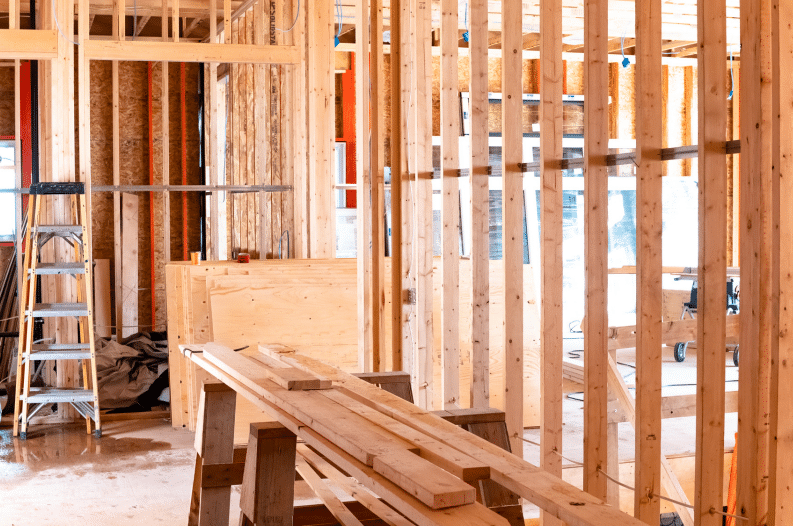
Prefabricated timber frame
Houses built using prefabricated timber frames will typically consist of a system of timber frame wall panels within the external walls. The frames carry the loads from the roof and upper floors and everything is supported on the foundations.
Similar to any other type of dwelling, the foundations will typically be of concrete and designed to suit the site conditions. A complete prefabricated solution will incorporate the roof trusses or roof panels, upper floors and internal and external wall panels in one package which is transported from the factory and assembled on site.
Prior to the delivery and assembly stage, the foundations will have been constructed along with any base walls or footings required. After the timber frame structure has been erected, work then begins on the external leafs of the external cavity walls and the roof covering is fixed according to the design.
It is important to remember that although prefabricated timber frame panels are factory produced, suggesting a degree of automation, most manufacturers still manufacture their panels by hand. They use automated equipment in the form of different types of powered saws and nail guns but only a few have installed fully automated panel manufacturing machinery.
Armed with the knowledge of the correct panel materials to use and how they should be put together, it is feasible that panels could be manufactured on a DIY basis. Such an approach would require that the panels be designed and then certified by a structural engineer, but if you had sufficient time and a suitable shed available, it is certainly achievable.
Structural considerations
The maximum permitted height of timber frame residential buildings has received a lot of attention over the past few years, but self-build homes of up to two storeys, with each storey having a typical floor to ceiling height of 2.4 metres, remain covered by standard building regulations.
Across the world, the limits which timber frame construction can attain are continually being stretched. At the time of writing, at 25 storeys and 86.6 metres high, the Ascent MKE Building in Milwaukee, Wisconsin, is the world’s tallest mass timber building. It was built using a framework of cross-laminated timber (CLT) and Glulam, with a concrete base, elevator and stair shafts.
As with all ‘tallest’ buildings, it will be surpassed by one planned for construction in Toronto at 90 metres high and then by a 100 metre tall residential building in Switzerland which is planned to complete in 2026. In reality, if a complex design means that external walls require multiple studs at relatively close intervals, then it can quite easily reach a point where a conventional timber frame is not the answer.
The building should use efficient framing techniques that minimise the total mass of timber to be used, so in some cases a hybrid solution that uses steel or engineered timber beams and columns along with the ordinary timber frames to achieve larger open spaces, can be the most efficient option.
One effect of using too much timber in external wall panels is that their perceived thermal insulation advantages can be diminished due to a high timber to void ratio.
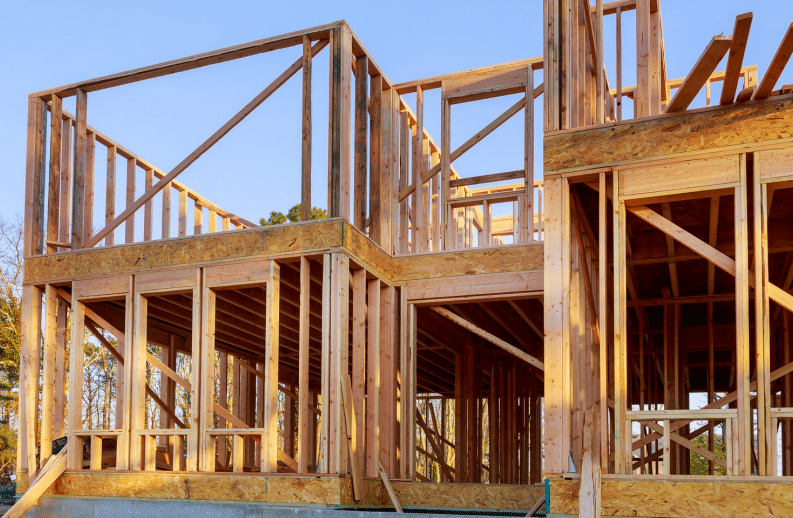
Environmental credentials
Which leads us to a persistent myth concerning the selling of prefabricated timber frame kits. Almost all of the timber frame manufacturers tend to cite the thermal insulation superiority of their timber frame walls over those built using traditional blockwork or brick methods.
This is misleading, as houses are all designed to the same energy efficiency standard so any properly designed and constructed thermal elements of the external structural envelope (i.e. walls, roofs and floors) will achieve the same levels of performance.
Also often quoted is the speed of construction, however any time saved on site should be compared to the time required to produce the frames in the factory and any order lead times which may apply.
The weather is frequently mentioned too, where construction of the timber frames can continue in the factory regardless of weather conditions; but when they get to site, just as for traditional builds, they should not be stacked, stored, erected or otherwise left standing incorrectly or unprotected in adverse weather conditions.
That said, timber frame construction does have the environmental upper hand over traditional bricks and mortar. A study commissioned by the Committee On Climate Change (CCC) in February 2019 concluded that a timber framed house had lower embodied carbon and also stored more sequestered carbon in the structural elements compared with a functionally equivalent masonry house.
It also should have lower levels of embodied energy, i.e. the energy required for the manufacture of the building components or materials, delivery to site and building.
Timber still has a way to go to become as truly sustainable as we would like it to be. According to an All Island study by Irish advisory body COFORD, over the entire island of Ireland the supply of timber falls short of the demand of the construction industry in volume terms. That includes sawmilled products and wood based panels.
And because timber grown in Ireland tends to be fast growing, many timber frame manufacturers import from slower growing regions, which yield stronger timber.
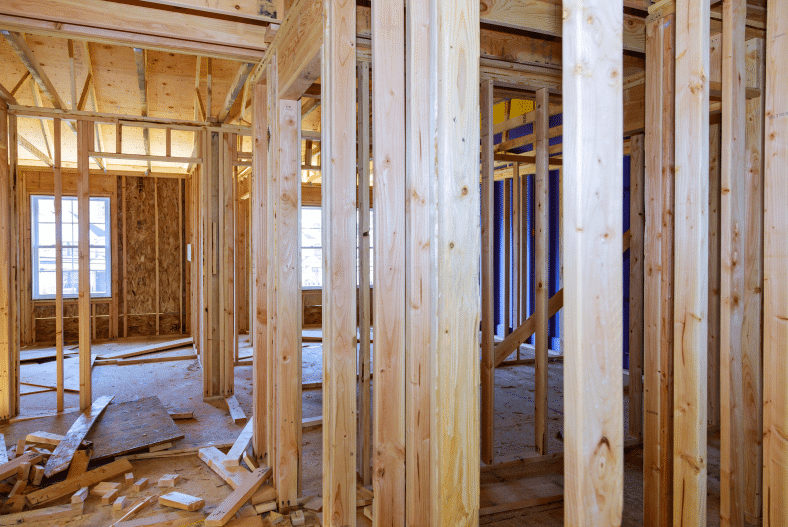
Life Cycle Assessment
Important factors in any Life Cycle Assessment (LCA) of timber would include the transport methods and distances between the forest, the sawmill, the timber merchant’s yard, the timber frame manufacturer’s factory and your site. Other important factors would include:
- The timber source, whether it is locally grown or imported.
- It should come from certified sustainable forestry resources.
- Timber plank production, treating and drying.
- Timber based sheet manufacturing processes. Use of reclaimed wood products.
- Are the timber products made in a low carbon manufacturing facility?
- Will the structure be assembled using removable fasteners to allow for potential reuse of the members?