A solid ground floor relies on the existing ground underneath to support it; this is how they’re made.
In this article we cover:
- What is a solid ground floor
- Details of subbase, hardcore underfill and blinding
- Radon barrier and dpm
- What is a subfloor and how it’s built
- Insulation layer details
- Mica and pyrite watchpoints
A solid ground floor should not be confused with the similar term solid floor which generally applies to any floor construction that does not contain hollow spaces or voids. Just to complicate things a little, a floor made up of precast hollowcore concrete slabs can also be described as solid.
The predesign site appraisal will allow the designer to not only decide on a suitable foundation design, but also to determine the best type of ground floor construction.
Let’s suppose that after clearing back the topsoil, you find that the existing ground is relatively level, dry and hard, does not contain features which may cause instability and no part of the building footprint will require more than 600mm of additional underfill to bring the ground floor to the level required.
In that case, a solid floor construction using a ground bearing concrete subfloor is most likely to be the easiest and most economical solution.
There are probably as many different methods of building solid ground floors as there are recipes for pizzas. But as a general rule, the floor will be typically built up in layers of a subbase and hardcore underfill. Then a dampproof membrane and/or radon barrier with concrete subfloor and insulation. Finally, the screed and floor finish. We will take each layer in turn.
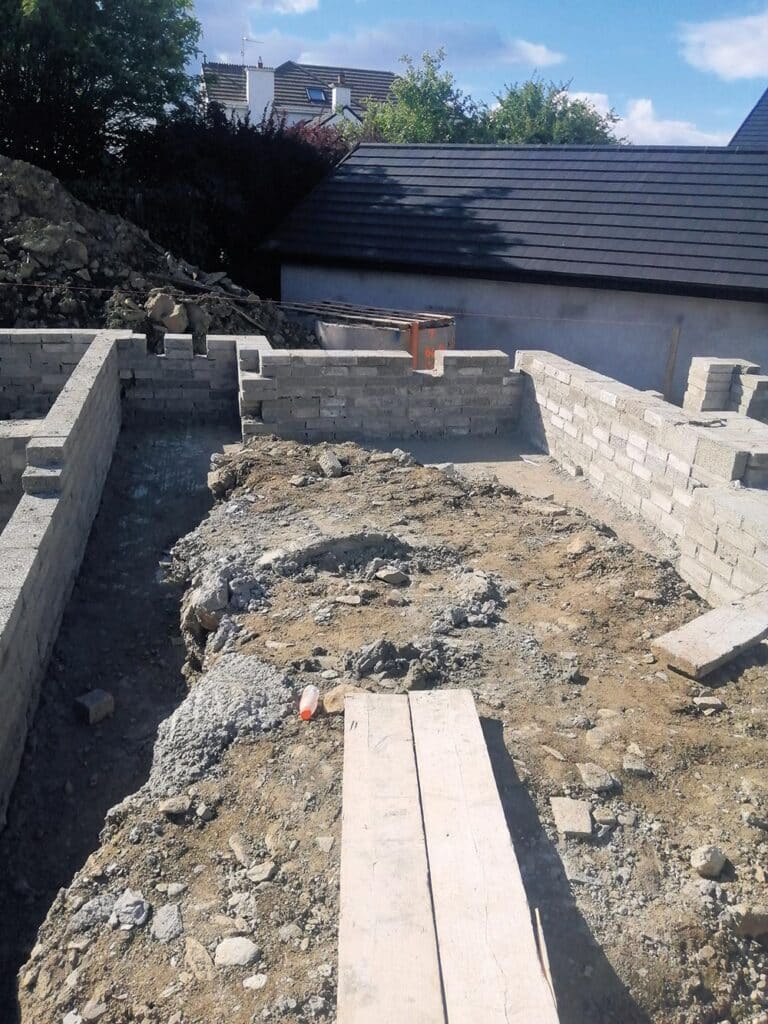
Subbase and hardcore underfill
A base of correctly graded and mechanically compacted quarried stone aggregate on top of the exposed subsoil is required to ensure that the building footprint has a level base with uniform loadbearing characteristics upon which to lay the solid ground floor.
The top 200mm should be gas permeable hardcore of 4mm to 40mm diameter and contain no small particles. Underneath this should be structural unbound granular fill material of an ‘all-in’ graded aggregate of up to 32mm diameter.
And below that it should be graded structural unbound granular fill material of up to 125mm diameter. The hardcore materials supplier must prepare and provide a Declaration of Performance (DoP) with every load dispatched to your site.
An underfill depth in excess of 600mm could result in undesirable settlement and therefore, instability of the floor above, even long after the building has been completed. If underfill is likely to exceed 600mm, it will usually be necessary to support the floor across the base walls and foundations, by constructing a reinforced concrete floor on site or by using precast reinforced concrete floor slabs.
Using precast slabs will have the advantage of avoiding the cost of laying an excessive depth of underfill whereas the onsite reinforced concrete floor will usually be faster.
To illustrate the consequences of ignoring the importance of underfill, I was called out not so many years ago to carry out a structural engineer’s survey on the solid concrete hall floor of a two year old bungalow.
This floor had collapsed in the night, with, in the words of the occupants, “an almighty bang, like an explosion”. As it turned out, the overly deep underlying base fill had been gradually settling over time and the resulting voids under the subfloor had enlarged to the point where the floor could no longer carry its own weight and failed catastrophically.
Luckily, apart from the fright experienced by the family, no one suffered any physical injury, but it was interesting to note that they had seen or heard nothing before that night to forewarn them of the structural failure.
I have also seen a number of less dramatic failures where the floor settles gradually. This usually comes with warning indicators showing up as cracked floor tiles, out of shape door openings, or gaps appearing between the bottom of the skirting boards and the floor surfaces. Dramatic or not, any such failure of a solid floor is nevertheless a costly thing to remedy and must be done correctly.
If you have onsite concrete to dispose of, recycled concrete aggregate may be used in certain situations as a substitute for hardcore, but check with your designer before you use it.
Big chunks of concrete or other masonry will not be acceptable as underfill for your floors, so it must be properly crushed and graded. Note that the practice of buying in recycled concrete hardcore from elsewhere ceases to become environmentally friendly when the carbon output and energy required from transport and processing outweighs that of buying ordinary fill material. In other words, check what distance it has to travel. Needless to say, any material which may deteriorate over time, such as timber, plastic, plaster or other general building site waste; should not be used in the underfill.
Blinding layer
This allows the surface of the hardcore base to be quickly and easily levelled and if the radon barrier is to be laid first, a 15mm to 25mm blinding layer of clean sand will help to avoid punctures occurring as heavy concrete is poured over it.
Radon barrier or damp proof membrane (dpm)
The designer will have worked out whether the building requires a radon barrier membrane and will specify it accordingly, along with any additional measures which may be required such as vents, sumps, ducts and mechanical ventilation.
The radon barrier, being impervious to gas, should also fulfil the role of the DPM to prevent damp from rising into the floor construction but it must be certified by an approved body in accordance with the building regulations.
Most importantly, a punctured radon barrier is no longer a radon barrier, so the utmost care must be taken during construction works to ensure that it remains undamaged. It must be laid to cover not only the base of the dwelling but it must also be continuous over the entire footprint of the building, extending through the outer face of the external walls.
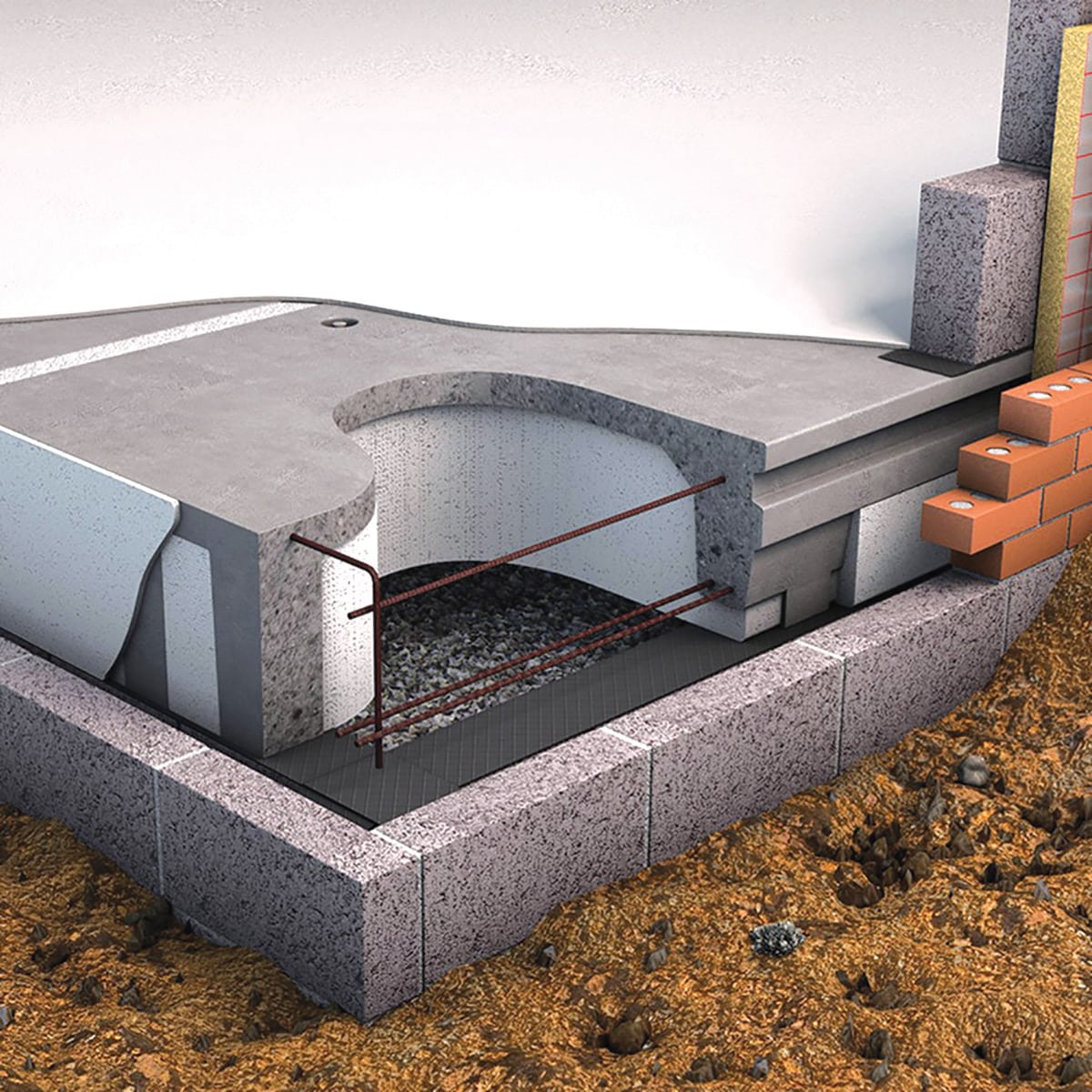
Any pipes or ducts passing through the barrier must be bonded to it using properly fitting ‘top hats’ and all joints in the barrier must be lapped and taped in accordance with the manufacturer’s instructions. Where walls are built below and above the barrier, continuous dampproof courses (DPCs) suitable for wall construction and approved by the necessary regulatory bodies must be laid over and be bonded to, the radon barrier.
A word of caution. Installation of a radon barrier and other measures is NOT a guarantee that radon gas concentrations in the building will be reduced to safe levels. Building owners must ensure that the radon concentration level is assessed when the building is in use and again after remediation action, should such prove necessary. Radon test kits are inexpensive, readily available and simple to use. See epa.ie (ROI) and ukradon.org (NI).
Subfloor
The subfloor provides the strength and stability for the whole floor. It also provides a base for most of the following construction works. It is usually made up for 100mm to 150mm of plain concrete but it can be made thicker and reinforced with either reinforcing bars or reinforcement mesh if there are any doubts about the underlying ground conditions or if the underfill exceeds 600mm in depth.
If internal solid brick or block walls are to be supported directly on top of it, localised reinforcement will also be needed. The design of any reinforced floor must be carried out by a structural engineer.
Know that, as with the familiar trend for unnecessarily sticking reinforcement into concrete foundations or floors in situations where they do not require it, there is also an unfortunate inclination to order over specified concrete ‘just in case’.
This can be costly, so the task of specifying a suitable concrete mix requires specialist knowledge and should be carried out by either your designer or by the structural engineer, who will specify the most economic solutions for you.
Some of the more environmentally friendly concrete mixes can have better thermal insulation qualities than ordinary concrete, so using one of those could reduce the amount of insulation required.
Insulation layer
The specification for this will be determined during the design process and the insulation will typically be a board type which can carry the floor loads above it without becoming compressed over time.
Most building projects now use foil backed polyisocyanurate (PIR) insulation boards (also known colloquially as ‘polyiso’ or ‘iso’) for floor insulation. There is a builder’s version of an urban myth whereby many seem to believe that they must always use PIR.
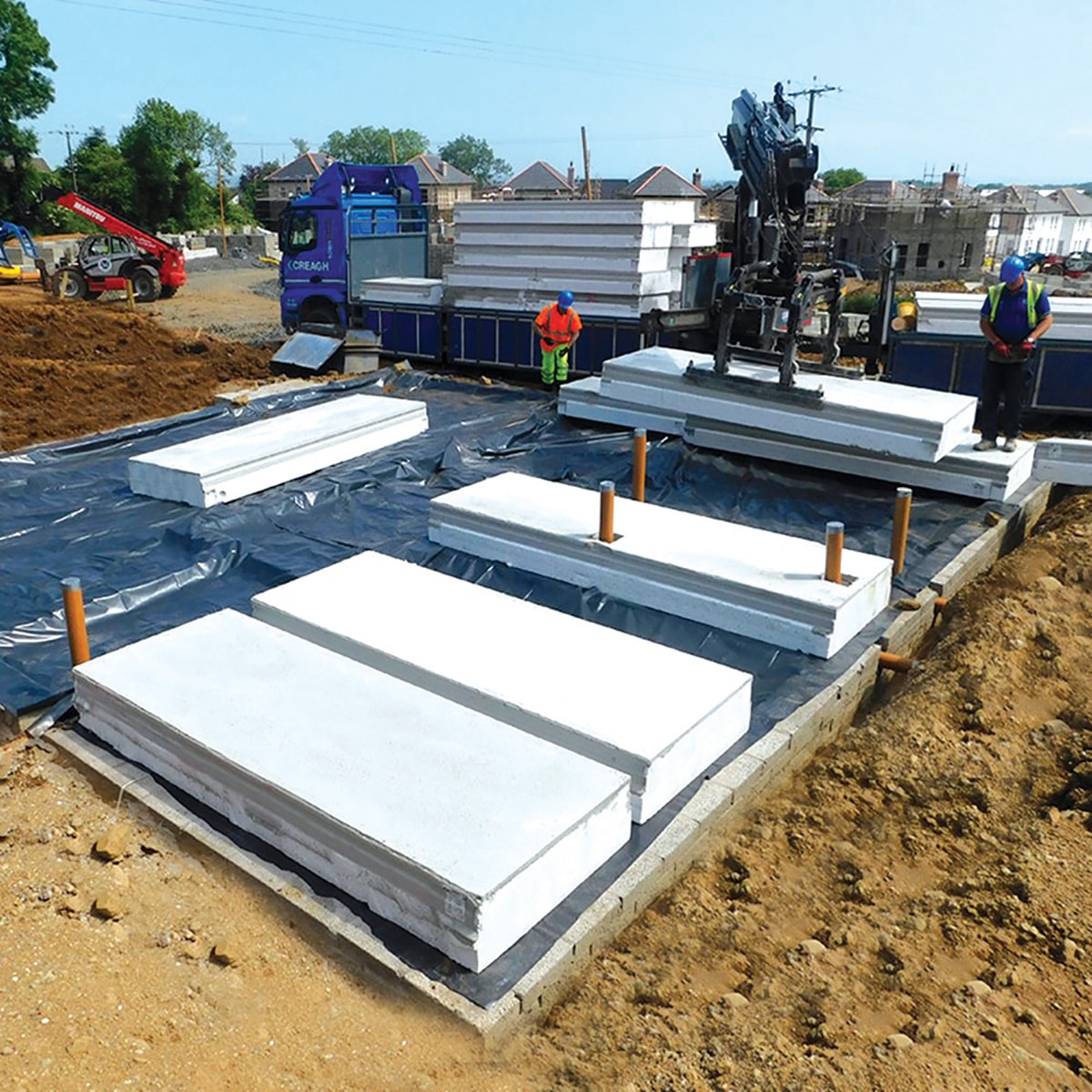
This is not the case, so do ask your designer whether a cheaper type of insulation will do the same job in terms of durability, moisture or condensation control, U-value and load carrying ability. A lower-cost option such as flooring grade extruded polystyrene (XPS) would need to be thicker than PIR to achieve a similar U-value, but if there is sufficient space to accommodate it within the overall floor thickness, then when properly specified and installed, there is no reason not to use it.
Other types of board insulation are available, so take time to explore the options under advice from your designer. Today, most board insulation manufacturers use foaming agents that don’t use chlorofluorocarbons (CFCs) or hydrochlorofluorocarbons (HCFCs), both of which are harmful to the earth’s ozone layer. But it’s better to check to make sure of what you are buying.
Mica & pyrite
Pyrite or iron pyrite is a common mineral that can be found as crystals in sedimentary and some metamorphic rocks. Because of its gold-like hue, it is otherwise known as Fool’s Gold. The presence of large amounts of pyrite in construction materials such as aggregates can cause those materials to expand, crack and disintegrate over time due to a chemical reaction when they are exposed to oxygen and moisture.
These processes can cause pyrite rich underfloor hardcore to lead to defects in walls and floors. Not only that, but a high presence of pyrite in the aggregate used to make concrete can lead to severe deterioration as the pyrite oxidises.
Replacement of faulty materials with ones that meet the new building standards appears to be the only practical solution, but can be very costly. This is another reason why the supplier’s DoP certificate is a requirement of the building regulations.
Mica
By now, everyone involved in the construction industry should be aware of the 2017 Irish Government report on defective concrete blockwork which affected thousands of homes across mainly the counties of Donegal, Sligo, Mayo and Clare. And now it seems, further afield.
The source of the problem was found to be a higher than normal amount of muscovite, also known as common mica, in concrete blocks. A presence of just 1 per cent of muscovite in the concrete apparently reduces the strength of the internal bonding by 5 per cent and also weakens the blocks’ bond strength with mortar.
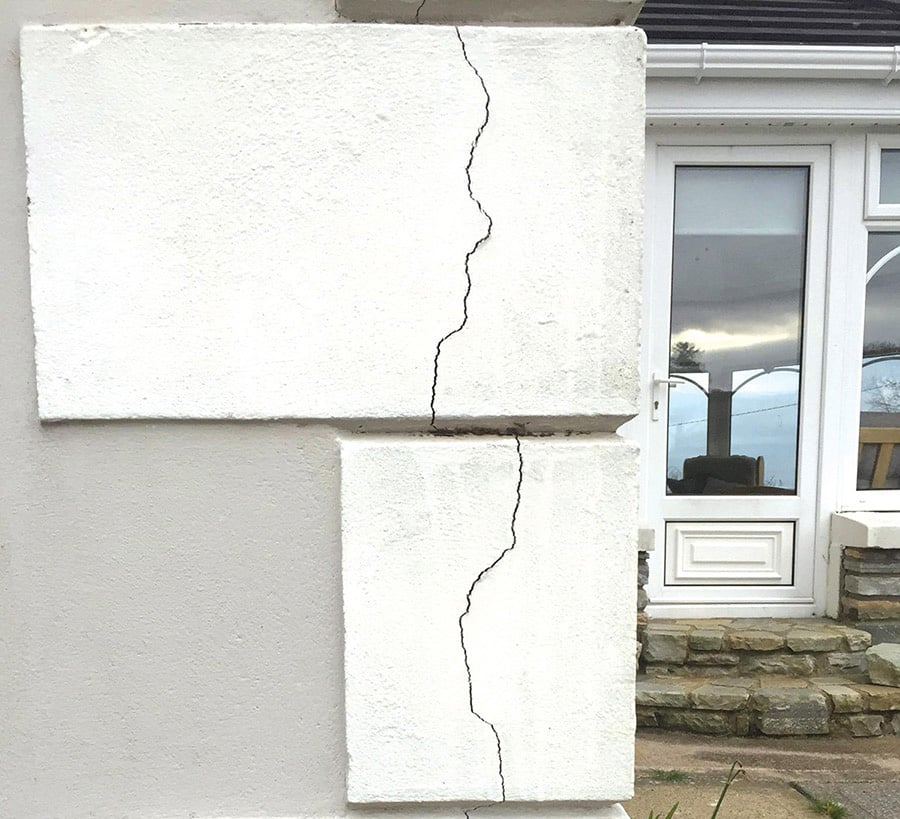
The mica can also absorb water which can lead to further damage to the blocks, due to winter freezing and thawing cycles. In some affected homes, the amount of mica in samples was found to be potentially up to 14 per cent, which is significantly above the 1 per cent limit accepted by the National Standards Authority of Ireland (NSAI).
Any companies producing building materials must comply with the regulations which are in place to avoid such problems as may be cause by the likes of mica and pyrite. The risks of non-compliance are now so potentially costly that any similar future scandals are highly unlikely, however all self-builders would be wise to actively seek evidence for the chain of custody (CoC) and a Declaration of Performance (DoP) for any building materials that they purchase.