What to check for on site when the timber frame kit arrives, from installation to building control requirements.
In this article we cover:
- Watchpoints on site
- What to do if issues arise
- Project management tips for this stage
- Information required by building control
- Role of the certifier
- Moisture management checklist
Moisture is the enemy of all timber frame construction, where leaks and trapped moisture can cause timber to rot and decay. The process of decay in timber needs three things; food (the timber itself), water and sufficient oxygen.
So whilst timber that is permanently wet and starved of oxygen, such as the famous timber piles in Venice, the Mary Rose, or our own bog oak; can survive intact for hundreds of years, timber that gets exposed to a combination of air and water will suffer.
Watchpoints
Not only are timber panels at risk during the delivery and handling phases, but after erection they can suffer from excess wetting. One of the greatest problems is that they get wet and are then covered over before they have time to dry out. Insulation will generally retain moisture for longer so select insulation that dries quickly and that doesn’t slump when wet.
Some design features are best avoided if they present a risk of trapping water. These could include flat roofs, parapet walls, balconies, level valleys between roofs, canopies on external walls and the like.
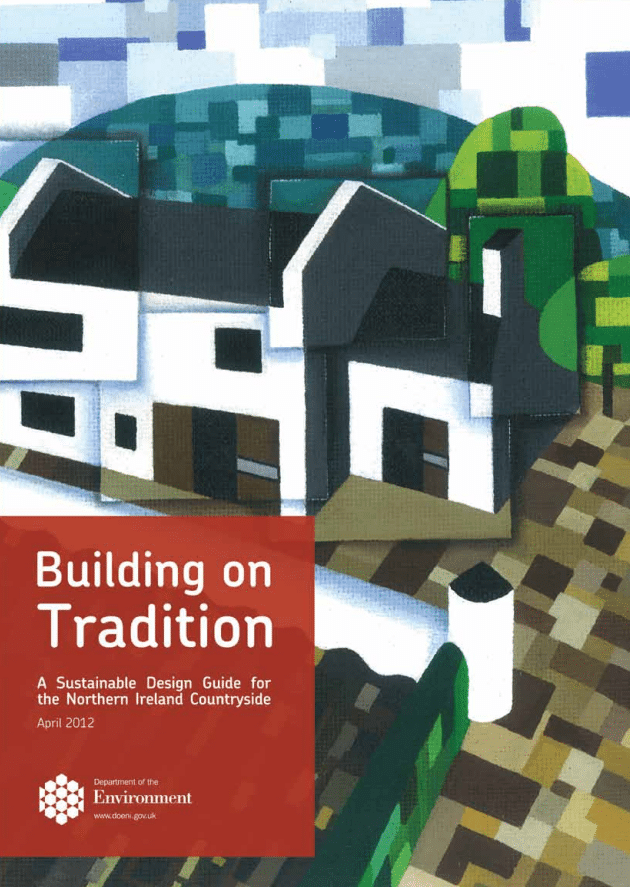
On site timber frame kit
Differential movement can also allow ingress of moisture through areas such as cracked render, gaps around windows and doors and so on. The main problem with leaks is that they tend to remain unnoticed until damage has already occurred.
Leaks during a building’s lifetime can also arise from plumbing, sanitary ware and heating systems, so regular maintenance of these fixtures is perhaps even more important in a timber frame home than traditionally built ones. Provided that the potential issues are taken care of at the design phase, then human error will be responsible for most problems during and after construction.
“Building control will require that you submit information in relation to your design.”
The old rule “if a thing can go wrong, it will go wrong” is too often confirmed by hard experience and it can be applied especially to the erection of prefabricated timber framed structures on site.
One golden rule to keep in mind is that everyone on site at any time for whatever reason, is responsible for correcting errors and no one should ever be allowed to claim “that wasn’t my job”.
If they cannot correct the error themselves, then they have a responsibility to report it to someone who can and will take the correct course of action. I have sometimes seen well made timber frame panels left out in very poor conditions such as standing in deep puddles of dirty water, or covered in snow, or stacked misshapenly at odd angles, or with badly torn breather membranes.
Anyone, from the truck driver, the telehandler operator, individual tradespeople, to the site foreman; should have intervened in these situations but failed to do so. Always remember that work completed by one trade should be left to an appropriate level of finish and in the correct state for other trades.
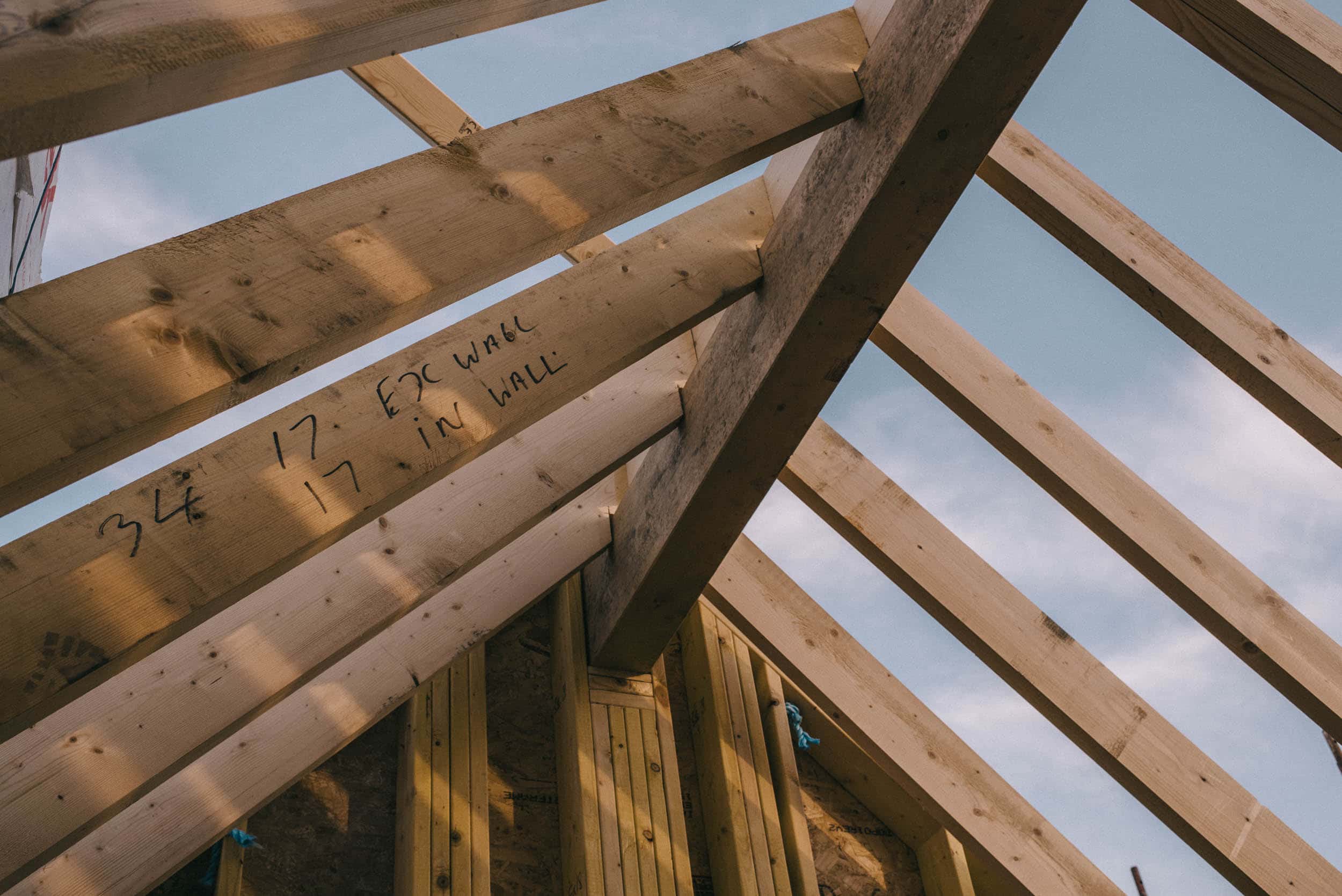
Information required by building control
Building control will require that you submit information in relation to your design. In NI they will carry out inspections during the build. Designs and specifications must be clearly understandable and include:
- A full set of working drawings including drawings produced by the timber frame manufacturer.
- The materials specification.
- The position and materials for cavity barriers in accordance with the building regulations.
- Manufacturers’ written recommendations relating to proprietary items.
The fixing schedule must accompany details of every connection required on the project, including those for structural connections, framing, wall ties, VPM, sheathing and VCL; and should show:
- The number and spacing of fixings, including nailing patterns and edge distances.
- The size and type of fixing, including material and corrosion protection.
- The method of fixing, for example, skew nailing.
Where wall design relies on plasterboard to take racking forces, the design should clearly show those walls include the type and spacing of fixings required.
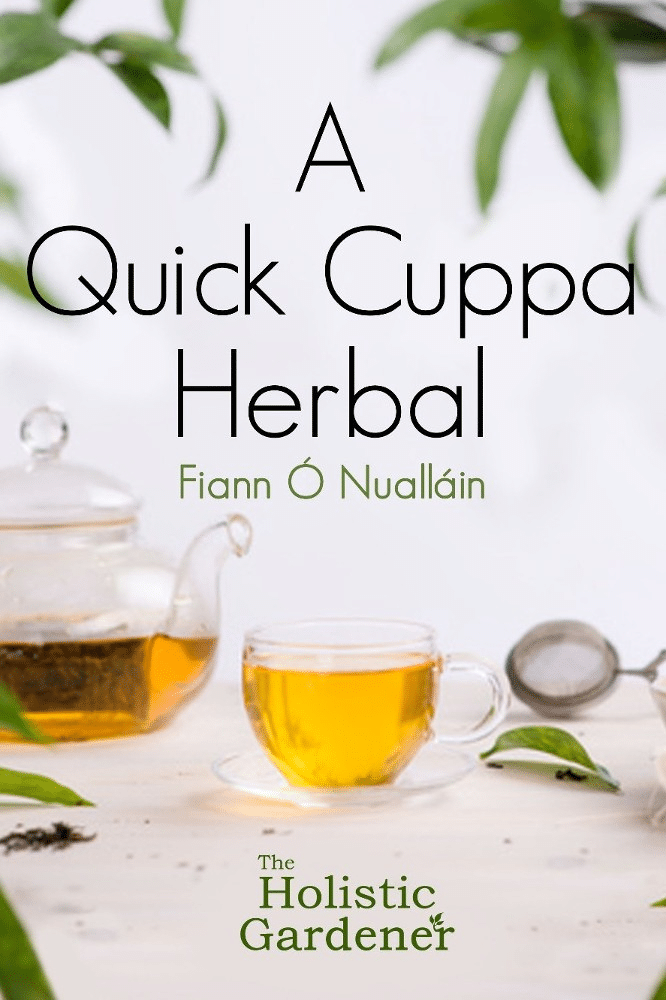
The design (and later the installation) of the timber frame structure should be checked and certified by a structural engineer and/or an NHBC registered timber frame certifier, who should not be the designer of the timber frame nor be from the same practice or company.
The certifier should complete and sign a certificate confirming assessment of structural adequacy for each specific project and give a copy to the builder and to building control.
Moisture Management Checklist
Solutions for the control of moisture should include:
1. Consider an open panel type of timber frame structure and get it inspected frequently by the certifier during construction.
2. Keep the bottom surfaces of sole plates for all external wall panels at least 150mm above the external ground level. This should include areas where the external ground rises towards entrance doors to comply with the access regulations.
3.Do not fix the sole plates of internal walls in positions where they will be left sitting in a potential water channel, e.g. where a floor screed and DPM is laid up along each side of the bottom of a wall panel.
4. Get the roof on and the building shell weathertight as soon as possible.
5.Consider putting up a temporary roof if the building is to be left exposed for prolonged periods in bad weather. The cost might be less expensive than the cost of remedial work.
6. Build the timber frame during dry weather. I know, that’s easier said than done, but if at all possible, try to make it happen.
7. Allow all wet timber including wood based panel products, to dry out properly before covering them.
8. Monitor the moisture content of all timber, wood based panel products and the insulation. The moisture content should be stable at less than 20 per cent before closing up any timber frame panels. Remember that water runs down, so timber at the bottoms of panels will probably be wetter than the timber above. Also, wood based panel products can retain moisture for longer than solid timber.
9. Use temporary membranes to keep out water ingress where possible and to protect sensitive materials during construction works. These might include wood based panel products such as OSB and plywood, all membranes, plasterboard, insulation, etc.
10. Don’t allow trades to nail through or otherwise make holes in the VCL or VPM.
11. Ensure that differential movement measures are built in accordance with the detailed drawings.