Thanks to advances in technology, there are plenty of modern construction methods available in Ireland to build new or extend.
In this article we cover:
- Structural Insulated Panels (SIPs): what it is and how to build with it
- Mass timber construction including Cross Laminated Timber (CLT): what it is and how to build with it
- Steel construction: when to use it and how to build with it
- Eco block construction, from hemp blocks to clay blocks: what they are and how to build with them
- Hybrid systems, from structural EPS to ceramic homes: what the options are and how to build with them
Most modern structural methods will involve a higher upfront cost to build the walls but will usually save on both labour and time on site.
The energy efficiency of the building will also help to balance the cost comparison – with modern methods you usually get the guarantee of an airtight and well insulated home as part of the package.
Here’s what’s on the menu.
Structural Insulated Panels (SIPs)
This method of construction, which is timber panel rather than timber frame, has long been used in North America, but it is a comparatively recent innovation in Europe. Instead of using timber to form a frame, SIPs consist of timber-based boarding, sandwiching sheets of rigid foam insulation such as expanded polystyrene.
The two materials are firmly bonded together so that they effectively act as a single structural component. The resulting panels are said to be five to ten times stronger than conventional timber frame. In Europe, they are used mainly for internal and external walls, although they are increasingly replacing rafters because they provide a clear roof space that can be used for bedrooms. The first SIP houses in Europe were built from panels shipped from America, but there are now factories in the UK, Ireland and the rest of Europe.
The insulation is more effective in comparison with other systems and masonry construction. In addition to this, the walls to SIP houses are relatively thin, freeing up more space for use in the rooms of the house – a factor that could be important on a cramped site. The relatively airtight construction is a major contribution to energy efficiency by reducing the amount of warm air escaping in winter.
On site a crane is needed to manoeuvre the panels into place and assembly on site is a job that is best left to specialists, who slot them together and seal the joints. The structure of an average sized house (e.g.150 sqm) can be assembled in two or three days. Cost wise if you choose a standard design, it should compare well to other methods that achieve good airtightness and insulation standards. However more common are bespoke designs which will inevitably come at a higher cost.
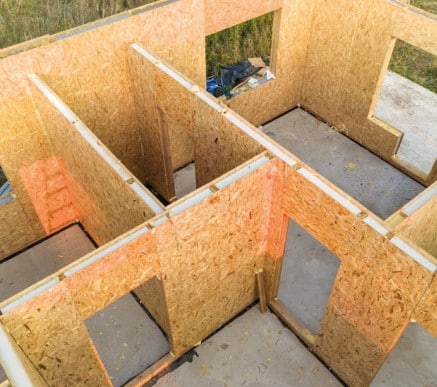
Mass timber
Timber as a material is structural, vapour permeable and renewable when sustainably sourced. To make it even stronger, engineers have developed a steel alternative that is known as glulam, which can replace steel supports (RSJs and the like) in domestic builds. This structural material is not only used as support beams, it can also become a whole house construction method (see page 128).
Cross laminated timber (CLT) is another innovation that’s come of out of timber R&D departments, consisting of planks of timber glued together and layered at right angles to produce a sandwich made up of three, five or seven layers which form solid timber panels 3.5m wide by up to 22m long. These huge sheets of CLT are then fed into an enormous CNC (computer numerical control) machine which uses precision engineering to cut the panels needed for your project.
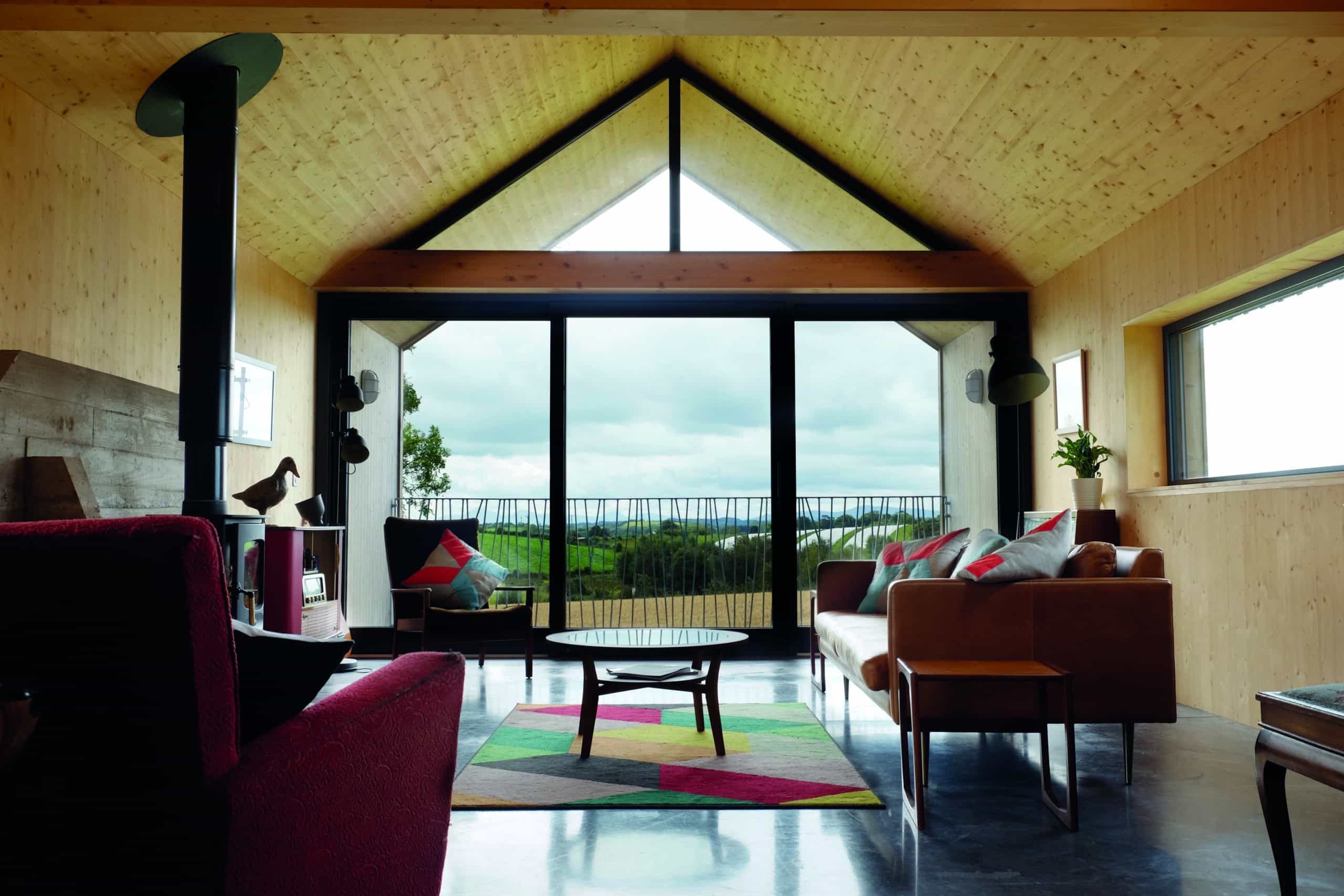
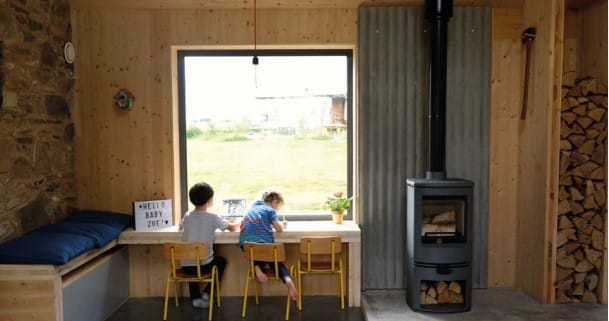
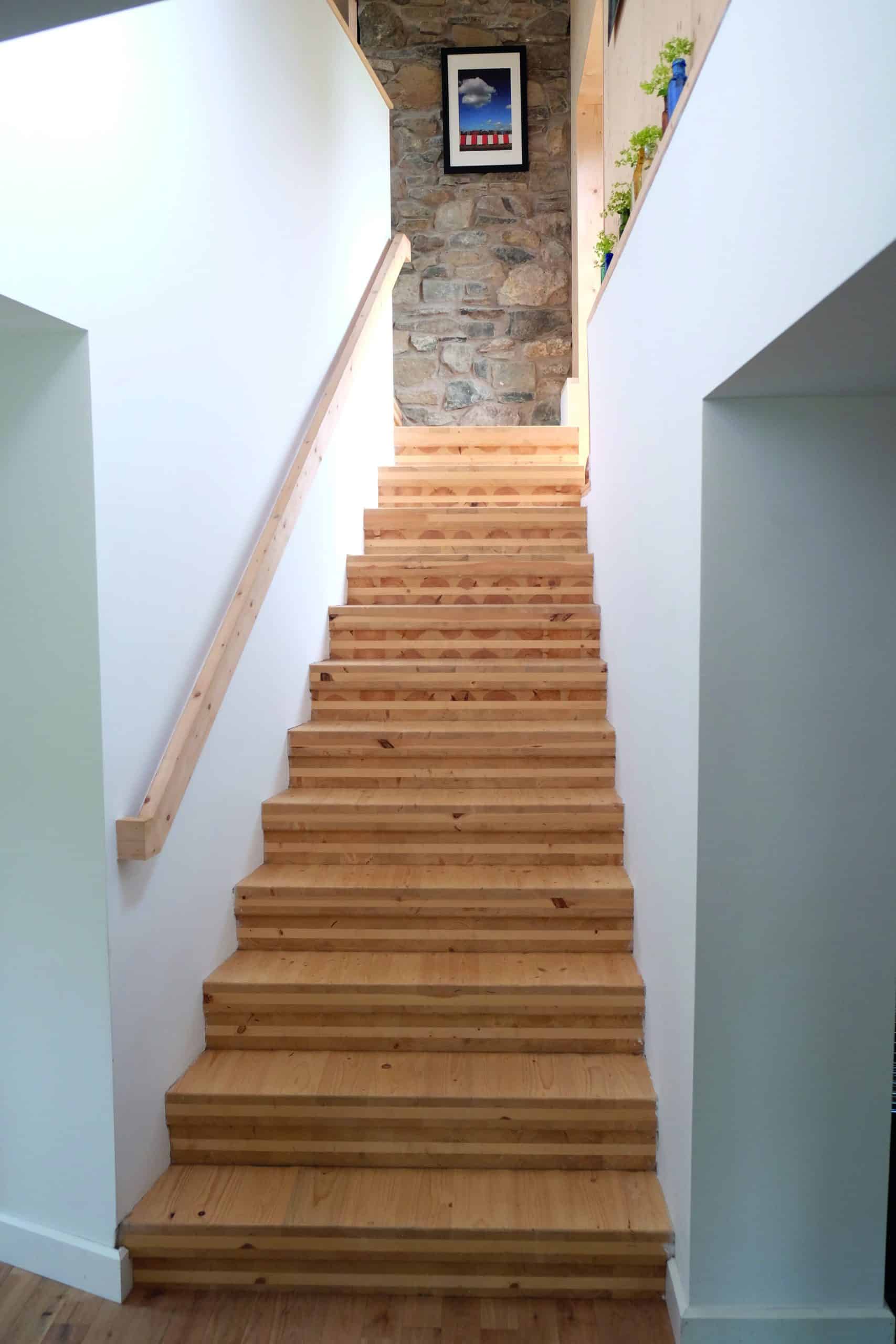
Doors and windows are simply cut out like cookie dough and even drilling out ducts for plumbing and wiring can be done in the factory before the panels are finally stacked on the back of a lorry in the correct order for assembly on site. The structure is then usually externally insulated and clad.
Professional input at both the design and construction stages is essential for either of the methods, so as to produce a design that plays to the strengths the material has to offer. CLT can create intricate roof forms, simple cantilevers and even lightweight structures placed on top of existing buildings.
In the case of CLT the erection of the panels is also a specialised process; they can weigh several tons and fixings must be accurate and correct for the structure to work. The builder then completes the insulation, roof and cladding as well as all the internal work. The waste, which is cut from the windows and doors in the factory, can be delivered to site along with the rest of the panels to be reused for anything from stairs to built-in or freestanding furniture.
Cross laminated timber (CLT) is another innovation that’s come of out of timber R&D departments
More expensive upfront than more traditional alternatives, building with glulam or CLT is quick as well as fire resistant (as with logs, the timber chars). Also, with every surface structural and solid, there is no need to look for studs or insert plugs before screwing something onto the wall.
Steel
The big advantage of steel is its design flexibility, so if your house is a simple design, then steel probably doesn’t add up cost wise, but anything more adventurous than this and it’s worth investigating. It is, for example, exceptionally easy (and thus comparatively cost effective) to create balconies and other structures that fall outside the building’s envelope. Steel frames are also a solution when working on uncertain ground, or when adding extra storeys to an existing building.
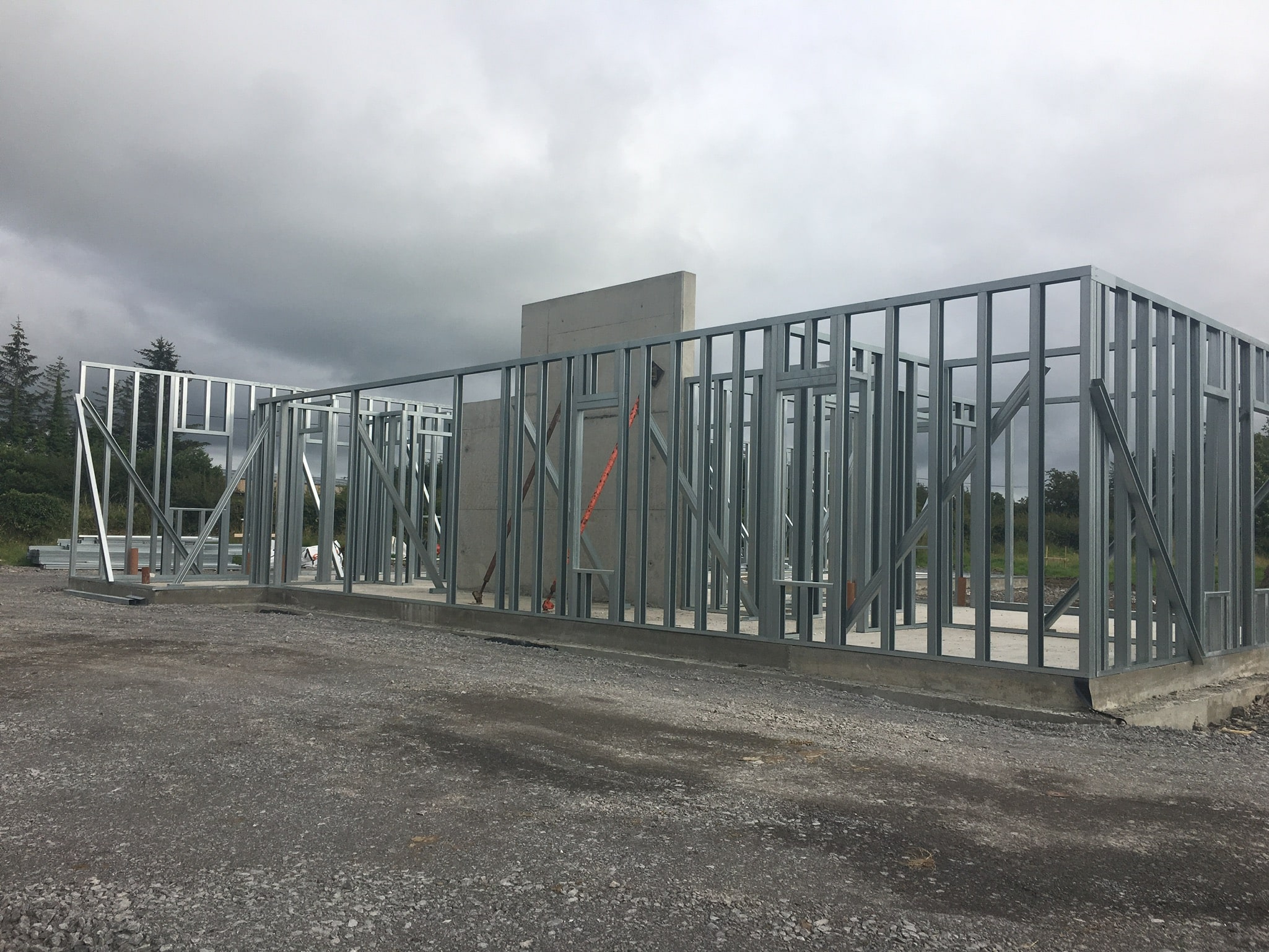
Warm frame construction, where the lightweight steel is enveloped in insulation in a way that ensures the dew point is outside the frame and thus minimises condensation, makes sure that nothing can rust.
The stick build method is what most people use (rather like a timber frame built from lengths of timber on site, only with light steel); there are also panelised systems, some of which can be pre-insulated and even have ties welded to the exterior surface to take brick or stonework. This type of system can be load-bearing, with the result that no rolled steel elements are required at all and its strength means that concrete upper floors are simple, cost-effective to create and able to accept loads within a day or so of placing the concrete.
Good steel frame companies will take your design, do all the engineering calculations for you and deliver a steel package that they, or others, can install. All the window and door openings are ready-made, and just about any level of pre-finishing complexity can be achieved to reduce work on site. There is a cost for this, but it could be the difference between building during the winter or not.
Steel framing doesn’t need treating with chemicals in the production process or later, (unlike timber), because it can’t become infested by worm or fungus, so no potential exposure to the chemicals that are sometimes emitted from treated timber. Steel also provides very accurate dimensions, hard to achieve with masonry skin, and provides the widest spans possible.
Steel roofs are also possible for specific shapes but in most instances trussed roofs (timber) are used as they are more cost effective.
Eco blocks
Engineered clay blocks and hemp blocks are structural materials that provide strength and insulation. As vapour permeable materials they allow moisture to escape all the while retaining heat within the walls. These tested and certified methods aim to take the hassle out of building with natural materials by providing a clear way for certifiers to sign off on your project. Compressed earth blocks are also factory made and offer similar advantages.
Hemp is usually combined with lime, which acts as a binder, hardener and preservative from rodents, fungi and microorganisms. As a finished material in walls, eco blocks are hygroscopic, which means they can absorb and release moisture to create an even indoor humidity, unlike many alternatives. They also have quite a low air permeability, one of the most important criteria in meeting our current building regulations. See also alternative building methods page 121.
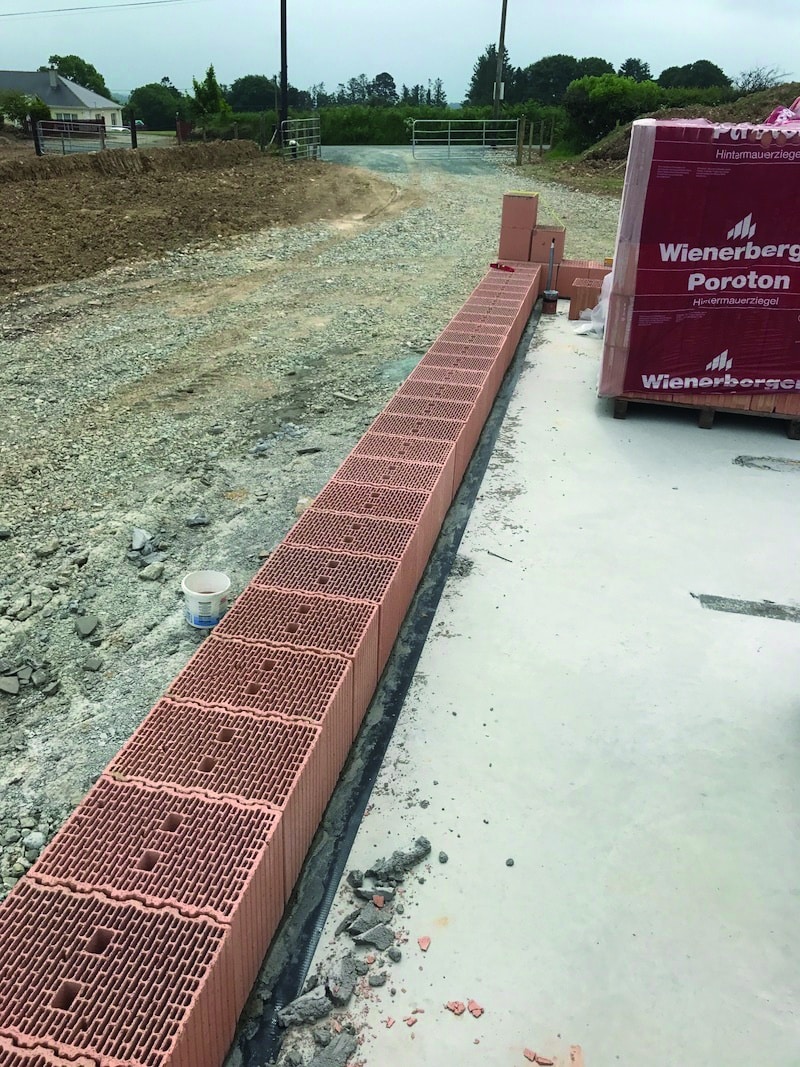
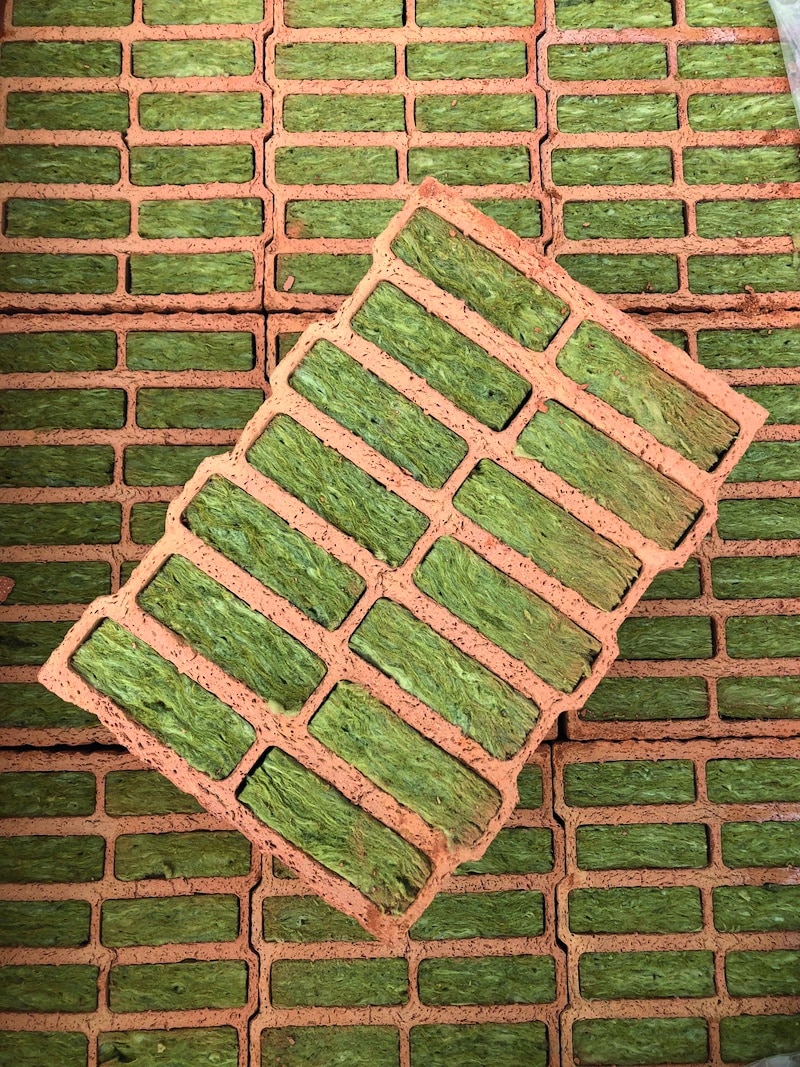
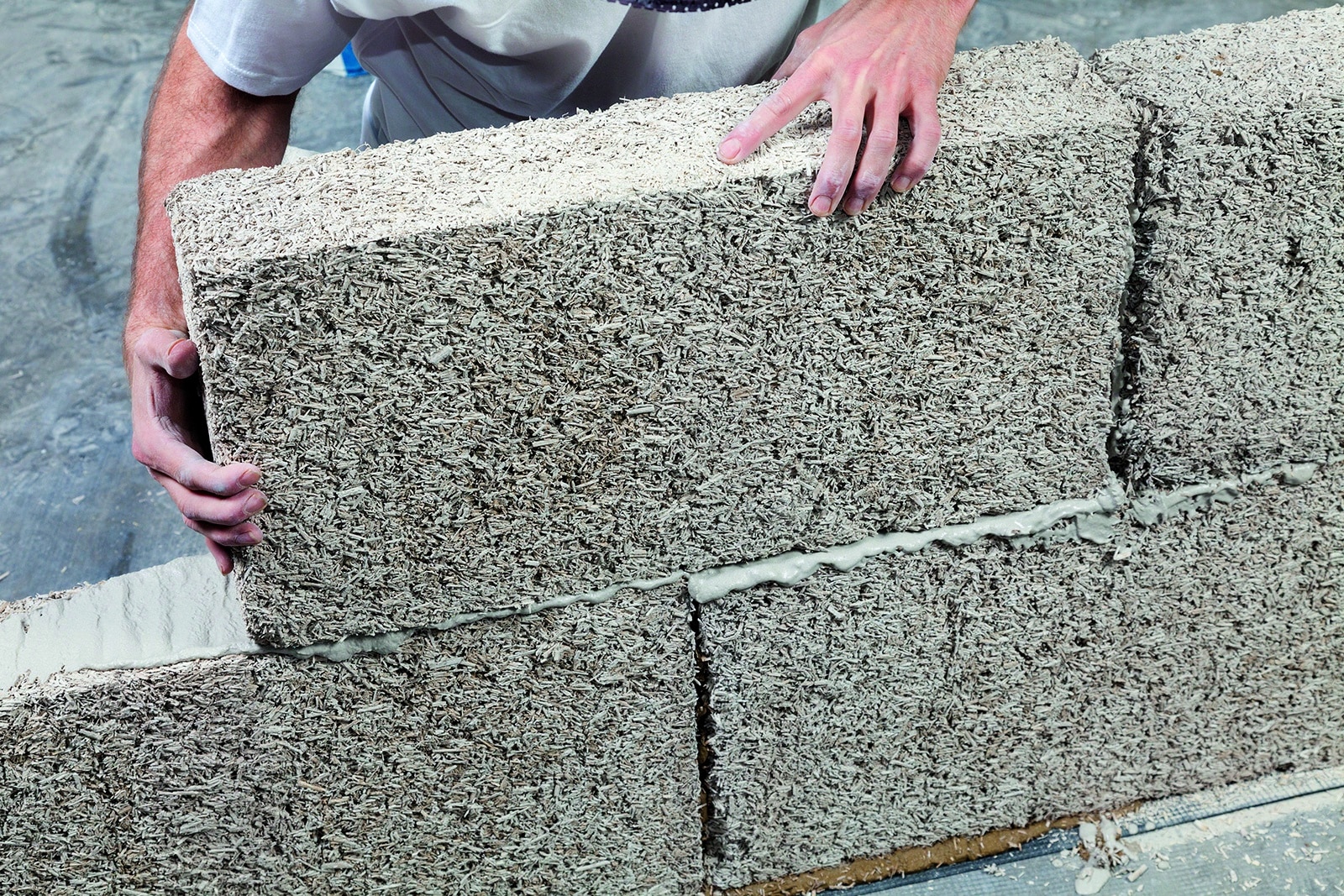
Hybrid systems
Structural systems that incorporate factory fitted insulation can include a mix of materials; these often include fibreglass and/ or cement to provide strength and come in boards or kits that are quick and easy to install on site.
Expanded Polystyrene (EPS) is the insulation used as the casing for ICF construction and is often used in hybrid systems too as it is lightweight, widely available and easy to work with. Even though it is not the best performing insulation, making it thicker allows it to achieve excellent U-values. An example of this is an EPS structural frame system.
Another hybrid system is a wall panels made of hemp and lime that comes prefabricated and assembled as other SIPs systems. Similarly, straw panels made in a factory are also now on the market offering vapour permeable insulation within a premade timber panel. These lock in together to form the walls.
As proprietary systems (unique to each manufacturer), the exact build up of these wall sandwiches will vary; some will include membranes to help with airtightness and humidity transfer for example. The build up will need to be checked by your independent certifier, be it your architectural designer or engineer to verify compliance with the building regulations.
One example of this is using the natural properties of ceramic to retain heat.
The cost of Brexit
Many of the panel and prefabricated systems come from abroad and those coming from, or transiting through, the UK will now have Brexit to contend with. In NI the flow of goods is expected to continue unhindered but crossing the border may result in added tariffs. Check with your supplier how they will be dealing with the situation and what additional fees may be applicable, if any.
Articles by Micah Jones, Andrew Stanway, Julian Owen, and Astrid Madsen