What the most common soil types in Ireland are, how to find out what your site contains and what types of foundations are suited for each.
In this article we cover:
- Soil types
- Evaluating the soil conditions on your site
- Foundations for different soil types
Soil is perhaps most commonly thought of as a varying mix of dirty stuff in which to grow your vegetables. But in construction terms, ‘soil’ can apply to any combination of rock, gravel, sand, clay, silt, peat and man-made or ‘filled’ ground.
To complicate matters further, very different soil types can be found next to each other in relatively small (site sized) areas.
Retreating glaciers following the last great Ice Age about 10,000 years ago created complex soil conditions and water features throughout much of Ireland’s countryside. Glacial till and gravel, sometimes very deep, forms the youngest rock landscapes, while the 1,780 million year old gneiss formations at Inishtrahull (Co Donegal) are the oldest.
Nowadays, many of the rural sites available to build on were chosen to avoid taking up valuable productive farmland. They are therefore often found to occupy boggy corners or sterile rocky slopes. Disused quarries, old farmyards and other so-called ‘brownfield’ lands are also frequently used for site locations. It’s therefore essential to get to grips with the soil conditions on your site before you start to build, and preferably before you even buy it!
That said, remember a site isn’t ‘bad’ simply because of its soil characteristics – these can in fact allow you to explore design options for your house which you might otherwise not have considered. At the very least, undesirable conditions should have driven the cost down so that you have more money to spend on your project.
Soil Types
Soil is classified by particle size, ‘silt’ will pass through a sieve mesh of 0.002mm to 0.06mm and ‘boulders’ are greater than 200mm in diameter. Soil is further described by its consistency, e.g. ‘homogeneous’ describes a soil which contains only one soil type and ‘fissured clay’ will break into multifaceted fragments along fissures.
Peat is formed over a very long period of time from decaying vegetable matter. It produces methane (CH4), a colourless, odourless and combustible gas, the volume of which will vary throughout the growing season. ‘Marsh gas’ and the ‘firedamp’ of coal mines are also chiefly methane. In the great outdoors, methane emissions tend to be negligible but when trapped under floors and within continuous foundations, can build up to dangerous levels. Methane is combustible/explosive in concentrations of between 5% to 15% in air.
Peat is classified as either amorphous (no recognisable plant content) or fibrous (plant remains present); neither of which are suitable for building on. You should be aware that peaty sites are frequently filled to achieve a better base, but if the peat was not first removed from under the area to be filled, the site must be properly ventilated to prevent gas problems before building can commence.
The failure to remove peat will also cause long-term settlement as the peat compresses and the perimeter of extensively filled land is known to bulge, leading to instability in tree root systems and other physical boundary features.
Peaty soil and the water running off it are acidic, so attention has to be given to the specification for any reinforced concrete that is in contact with it. Sometimes the peat is not very deep and may simply be covering good stiff clay or even rock, so it can, on occasion, be fairly economical to remove it and find a base to build on.
Marshes and boglands are often associated with low-lying sites, but can frequently be found in upland areas. A rural site situated on a high watershed (which acts as the source for surrounding streams running down to lower land) can pose particular problems, especially for the discharge of wastewater. Similar problems are likely to affect a site situated within a closed drainage basin, i.e. where it is low compared to the level of the surrounding land. Water entering a closed drainage basin can only escape underground through streams or sink-holes for instance, otherwise it would be a lough! A study of historic mapping can also sometimes reveal areas that were once open loughs but are now marshland, so it would be expected that silt or silty clay will be present.
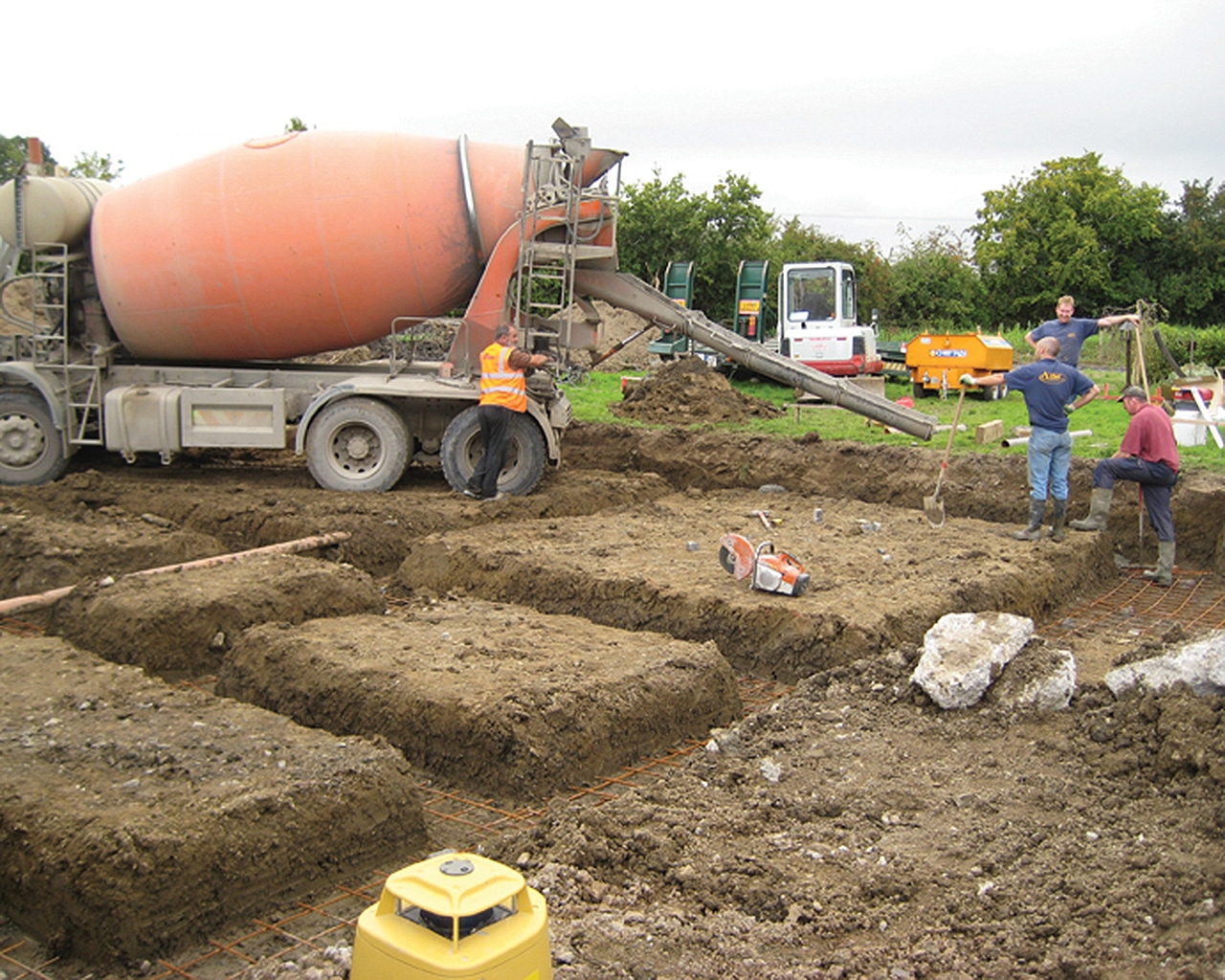
A drainage remedy had to be found for a client whose site was located on an upland watershed. The design solution was to construct a five-stage system which collected and then treated the wastewater by aeration, pumped it uphill to a reed bed filter and discharged it by gravity to a soil filter mound, after which the root systems of a dedicated tree planting scheme finished off the process. Proving that it would work was the difficult part for me!
Note that wetlands both inland and on coastal areas are frequently home to an abundance of flora and fauna species, some of which, such as newts, may be endangered and/or protected; if you find any on site you must declare it to the relevant statutory body (NIEA or EPA).
Sandy soil is found in localised zones throughout the country, especially in drumlin and coastal areas, and much of it is found intermingling with gravel. Quite often the presence of sand or gravel quarries in a locality will give sufficient indication that further site investigation is needed.
If a site is composed of undisturbed sandy soil of a consistent quality, then a simple raft foundation can provide a very economical solution. However loose, wet sand imposes high lateral loads on footings and retaining walls, resulting in extra costs for the siteworks or substructure elements of a build. In external siteworks, it will be necessary to reinforce sandy embankments to prevent erosion and provide surface strength using geotextiles and/or planting.
‘Running sand’ is a colloquial term describing sand which is behaving as a fluid. It can be a very localised phenomenon, not just restricted to predominantly sandy sites and is discovered during excavations where the sand starts to slip or ‘run’ into adjacent voids. The big problem is calculating how much of it there is and when it will stop. The best solution is to avoid it, but if unavoidable, stabilisation products can be introduced.
Clay soils have any number of descriptive names. The printable ones such as “expansive”, “shrinkable” and “heavable” give us a clue as to how clay behaves. Water content is the major factor which determines the nature of clay soils, but sand/silt content is also important. Clays range in hardness from “stiff clay” which cannot be moulded in the fingers and requires a pick for excavation; to “silty clay” which exudes between your fingers when squeezed in the fist. Some silty clays will even deteriorate rapidly upon exposure to air whereas hard or stiff clay is usually not a problem to build on.
Some contractors can have an overly optimistic belief in the load-bearing capacity of soft clay. I was once called out to a site to check foundation trenches, which on first impression looked OK, but I was a bit suspicious of the unnatural looking bottom in some of them. When the digger operator was asked to apply a bit of pressure with the bucket on the trench bottom, the ground quivered. Apparently the trenches had been going too deep for the contractor’s liking and he quite absurdly decided to cover the suspect soil with stones in an attempt to avoid extra underbuilding costs. The solution was to keep digging and a hard bottom was eventually found.
That said, while difficult, it is possible to build successfully and safely on soft clay soils if a stable moisture content can be maintained or if the building can be insulated from any soil volume change that occurs.
On all clay soils, you must also be made aware of the future effects of site drainage, tree removal or growth, subsequent construction, earthworks, etc., all of which will create changes in its behaviour. ‘Pre-draining’ a wet clay site is not a good idea unless it can be left to settle for a long period of time (at least a year). Also, thought must be given at the design stage to how neighbouring land will affect your site and if so, how to prevent it from doing damage. Is it likely for instance to increase water table levels during rainy times or drain water from you in dry weather?
As has been experienced on many rural sites where wastewater has been discharged to subsoil ‘filter’ systems, natural drainage is not a feature of most clay soils and the systems eventually clog up, resulting in expensive remedial works. The solution is to carry out soil percolation tests first (see box), then use the results to design a proper system.
Most rocky soil is fine to build on and can reduce the amount of excavation and concrete needed if it lies close to the intended subfloor level. On the other hand, a site where the footprint of the dwelling covers both rock and softer soils poses a challenge to the foundation designer. This is because different soils will carry dissimilar loads, but concrete strip foundations and the walls they carry are inflexible and will crack in areas where there is a sudden change in soil quality, thus leading to all of the problems associated with subsidence.
If rocks or boulders are found when digging out a site which consists otherwise of clay, the best thing to do is to remove the boulders. If voids are discovered they should be left to be filled with a weak mix concrete as opposed to filling with loose gravel; in the event of rainwater filling it up, hire a pump to get it out before pouring concrete.
In a situation where only part of your house foundations rest on solid rock and the rock drops steeply away under soft soil in other parts, the foundations will need to be designed so that there will be no differential movement.
It is interesting to note that we actually have a diverse range of rock types throughout our countryside, with Karst regions probably presenting the toughest challenges to construction. These regions of limestone, dolomite or chalk can contain sink-holes, (some of which may well be filled with peat or silt), underground voids and caves, cracks, crevasses and important
aquifers. They are therefore sensitive to pollution and will require detailed geotechnical surveys before building.
Underground sloping rock can be quite a surprise during foundation excavations, where the foundation base drops away sharply and the decision has to be made as to whether it is a good idea to keep digging (thus needing a lot of concrete) or to consider another solution. Thinly stratified rock (where rock is layered over softer soil) can also lead to nasty surprises if it is not discovered in time. A good site survey will ensure that trial pits are taken down far enough to identify these situations.
Iron ore in rock is fairly common but is not a structural problem. It does cause red coloured groundwater (locally called ‘spa’ water) and silt which can easily discolour construction materials and acts as a binder for some fine silts, easily clogging drainage pipes. Where you might want to conceal unattractive rock or scree slopes, hydro seeding is a useful solution which uses a slurry of seed and other mulch material to rapidly grow vegetation where it would be difficult to use more traditional horticultural methods.
The designer’s risk assessment is of crucial importance in cases where contaminated soil might be found. The soil can be contaminated from exposure to pollution caused by industrial processes, by-products within brownfield sites, or indeed surface water run-off (i.e. petrol from roads or industrial sites). Where diversionary drainage is not viable, geotextile filter layers can be used to separate out the polluted water and redirect it to a treatment area. Land which has been filled with soil from elsewhere must also be treated with caution, as some solid site ‘fill’ material can also contain organic matter which will create contaminated soil conditions and leachates.
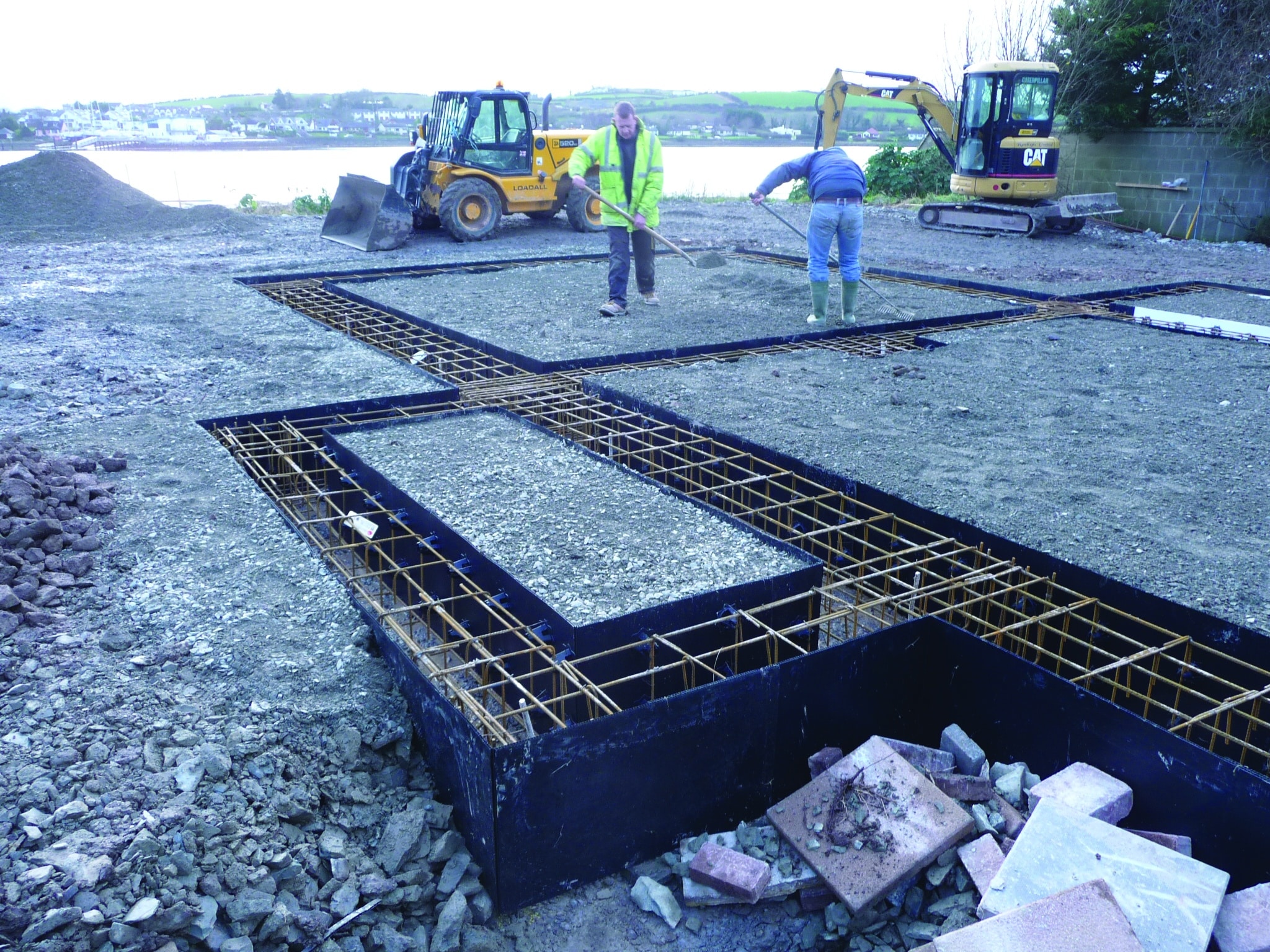
In NI and ROI, most instances of contaminated soil in rural sites will be related to agricultural processes and illegal dumping although some former industrial sites can and have been built on too. One of the problems with contaminated soil is that the presence of acids, chloride and soluble sulphates will affect the foundations and other structural metallic components. In many instances, soils can be successfully treated and retained as an engineering material using chemical stabilisation products. In landscaping schemes on brownfield sites, it is possible to plant new trees and shrubs in protective containers where the soil is badly contaminated and it has been decided to leave it undisturbed.
Evaluating the soil conditions on your site
When visiting your site for the first time, it is unlikely that trial pits or trenches will be provided so you need to go on first impressions and carry out a visual examination.
Visual examination
A good tip for soil type recognition is to walk around the site and look at the vegetation – what grows there will tell you a lot about the nature of the soil near the surface.
The presence of heather and spruce should indicate peat, high proportions of rushes and alder will indicate clay; and gorse or broom will tell you that there is dry sand/gravel soil. Marshland doesn’t need many clues but if you spot plants such as bulrushes, reeds or irises in an otherwise dry-looking field, then have a closer look. Most ferns like moist shady areas and willows generally like wet soil.
Be also aware of the many confusing variations in our countryside landscape where you can see gorse on raised dry ditches around heather-clad boggy land, or an abundance of silver birch (which many people associate with bogs – hence the idiomatic name ‘bog birch’) on perfectly good soil. The implication here is to use your visual examination as a guide to what might need to be checked out in more detail; and very importantly, at the correct depth.
After that, a preliminary risk assessment should be carried out by your designer, which should include at least the following:
• Local knowledge; talking to the neighbours will often reveal information that was never officially recorded and can tell you much about the historical use of the site, seasonal and historical flooding, etc.
• Aerial photography and drainage pattern maps.
• A study of the geological maps of the local and general area.
• A comparison between present and historical Ordnance Survey mapping.
• Details of any previous soil study data on, or adjacent to, the site area.
Trial pits and trenches
Any qualms about the site conditions must be answered at the earliest possible stage, ideally even before the site is purchased. Even ‘greenfield’ sites can conceal underlying pockets of
deep peat, so preliminary inspection trenches or ‘trial pits’ near the intended foundation positions should be dug out to determine what lies below the surface. This is something that engineers develop a feel for over many years so you’ll need to rely on their expertise regarding the position and depth of the test excavations, most of which will need to be carried out using a mechanical excavator.
Before deciding on an appropriate form of site investigation, the engineer will have established the position of the building and the foundation loads. If it is deemed apt to begin with trial excavations, they must be taken down to the proper depth. For shallow foundations, the correct depth is at least 1.5 times the width of the loaded area. The loaded area is taken to mean either the width of a footing, the width of a raft or the width of the building if the foundation spacing is less than three times its width.
For large buildings where bedrock is required to carry the loads, then the investigation must be taken down 3m beyond the top of the bedrock to ensure that the rock layer is sufficiently thick. On most sites for the average dwelling, the simple rule is to keep digging until a suitable base is found, and if this isn’t achieved within the reach limit of the excavator from existing ground level or if still digging at a depth of much more than 3m, then a piled or raft foundation must be considered (simple poured concrete foundations are likely to then become uneconomic in relation to piles).
If the soil conditions are found to be very unusual, a geotechnical engineer can then be called in to run tests to provide data on the load-bearing capacity of the soil which can then be used to ‘prove’ the adequacy of the structural engineer’s foundation design. These tests can require the use of boreholes, driving pegs or test piles, and additional trial pits.
Find your footing
he big questions when faced with tricky soil conditions are how to design the foundations, drainage and any retaining walls. This is frequently left unplanned until construction begins (a typical ‘easy’ approach is to show only standard ‘strip’ foundations on the working drawings) but this leaves you with an unknown element in your building costs – the difference between simple continuous strip foundations on ‘good soil’ and deep piled foundations on ‘bad soil’ can be as much as £5,000/€5,500 to £10,000/€11,000 or more for a typical house!
Foundations must be appropriate to the building type, in other words, a large building will need larger and deeper foundations than a small light structure. Where the soil type changes over a relatively small area, it can sometimes be feasible to ‘bridge over’ the obstruction or weak point using reinforced concrete.
Due to a scarcity of suitable ground conditions for them, raft foundations are unusual in many parts of our countryside so other foundation solutions such as trench fill or piles, can be found to be the best option. Strip foundations are suited to ‘low-rise’ buildings and pad foundations are typically used to support columns. Strip foundations and pads will not usually be taken down to depths of much more than 3m for reasons of economy, and together with rafts are described as ‘shallow’ foundations. Minimum depths (typically 600mm) are required to avoid the adverse effects of frost. Foundation depths to prevent damage from tree roots must also be correctly specified.
A strip foundation can be ‘trench filled’ whereby the trench is filled with a lean mix concrete and the strip foundation created closer to ground level, instead of creating additional hazards, i.e. lifting concrete blocks down to bricklayers working in a deep trench to build footings up from a strip foundation. The width of strip foundations must be designed so that the soil type adequately carries the weight of the building. A light structure on a good solid base could in theory use strip foundations which are just equal in width to the thickness of the wall, whereas a heavier structure on soft soil will require wide strip foundations. Foundations for retaining walls act as an integral component of the retaining wall, so need to be designed as such.
Where very wide strip foundations are required, it can be more economical to use a raft instead. A floating or buoyant raft is designed to float on a soft base and a surface raft relies on adequate soil bearing capacity for support.
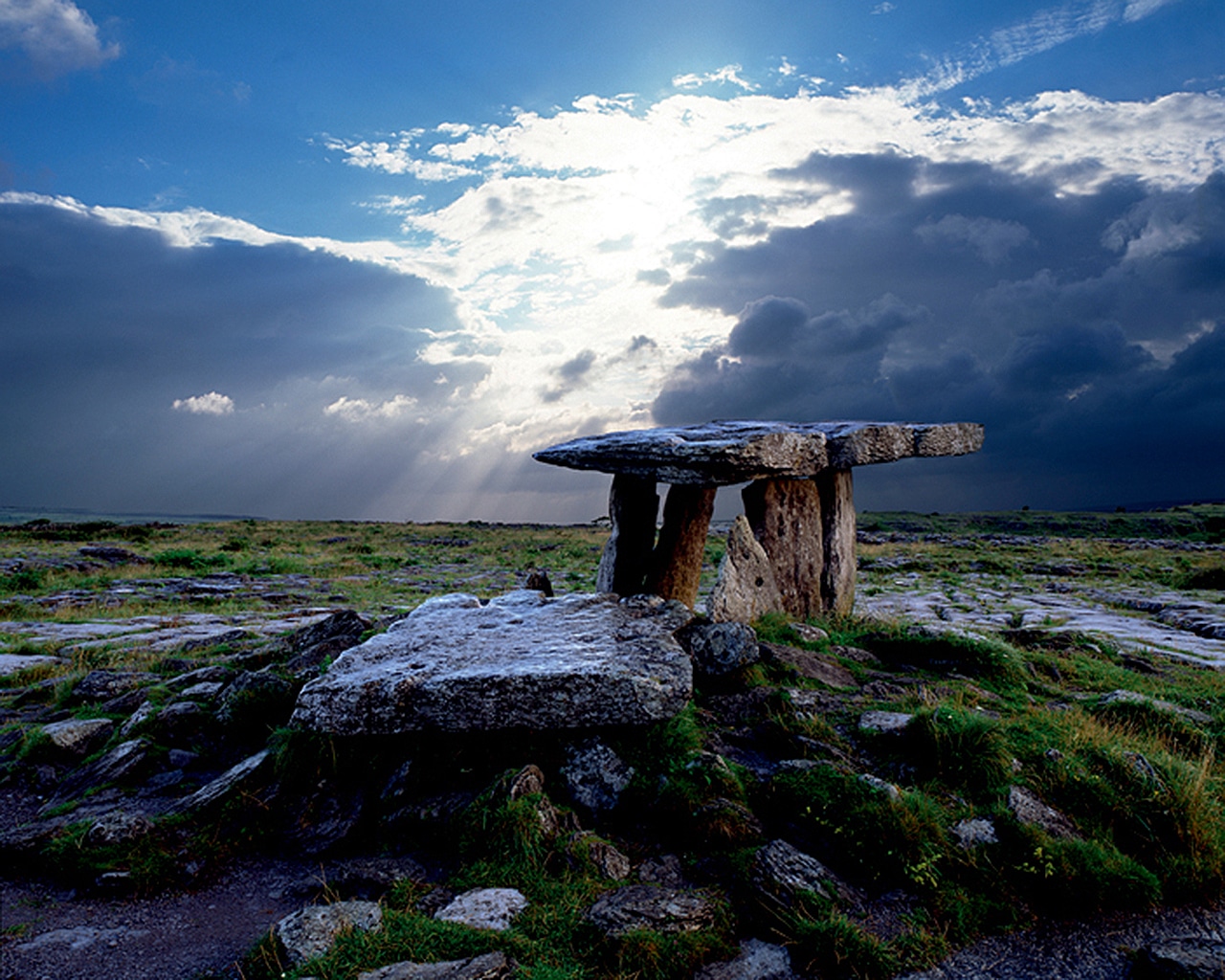
Piled foundations are described as ‘deep’ foundations and can vary enormously in dimension (5m to 100m in length and 75mm to 2,000mm in diameter). Small piles will usually be bored or drilled and the concrete poured into the hole, medium piles are frequently of reinforced pre-cast concrete whilst larger piles are typically steel. Medium and large piles are usually ‘rammed’ into the ground. Friction piles rely on friction build-up between the soil and the pile surfaces to remain in place and bearing piles are carried directly on or into a hard underground stratum.
Wastewater (the upmarket name for sewage) can prove costly to deal with on problem soils, especially marshy ones. There are situations where it is difficult or impossible to gain consent to discharge it into waterways, so the only solution is to create a system which does not allow effluent to escape off site. The ostensibly obvious solution would be to build a dedicated drainage scheme, but it’s not always a good idea if buildings are over or close to an area containing clay soils. Groundwater can also rapidly erode newly exposed soft soils which will create sediment build-up in standard drainage systems. Careful attention to the drainage design is required to avoid or cope with this.
Finally, remember that in the not-so-distant past, buildings were not built as airtight as they are today and underground gases such as methane, from peaty soils, and radon, from water, soil and rocks, could easily find a way to escape the building through draughts. With tighter building regulations relating to energy performance, this is no longer the case. Special care must therefore be taken to prevent gases from being trapped within the building ‘envelope’, that is, be allowed to escape from below the dwelling to the external air thanks to appropriate foundation design and mandatory gas barriers (as part of the damp proofing).
The descriptions of soil and foundation types are given here for general information and guidance and should under no circumstances be used to design foundations. Always use a professional engineer. NB: There have been some horrific accidents on building sites where excavations have suddenly collapsed, resulting in death or serious injury. It is your responsibility to prevent these through health and safety measures. See www.hsa.ie (ROI) www.hseni.gov.uk (NI).