Building your walls out of concrete will usually take the form of the ever popular block build, but there are other options to consider.
In this article we cover:
- What is concrete and how it’s greening its image
- What is cavity wall construction (blockwork)
- How to insulate blockwork walls
- Different types of blocks, from aerated to clay, standard size
- Single skin construction
- Cast concrete including flooring
- Insulating Concrete Formwork construction
In Ireland today, the most common building method remains concrete. What is it, how is it used to build walls and what are the pros and cons?
What is concrete?
Concrete is made up of cement, water and aggregates, often a mixture of crushed rock and materials that enhance its thermal and/or eco credentials. Not to be confused with mortar, which is cement mixed with water, lime and sand. Concrete can be mixed on site in a cement mixer for small batches, it can be brought on site in a cement truck to be poured, or can come to the building site precast in a specific shape.
Concrete as a building material is often part and parcel of a self-build. In the majority of cases, it is the primary material you will use for your foundations. Your floors and screeds, window sills and lintels, and even perhaps your roof covering, might also be made of concrete.
Because masonry is so commonly used in Irish domestic building, almost every building contractor has tradesmen at his disposal who can do a professional job. Many masonry materials are manufactured locally and are readily available from local builders’ merchants. Meanwhile lenders, insurers and warranty providers are comfortable with extending credit or cover for concrete builds.
Concrete is a strong material that boasts excellent fire and acoustic properties. It’s long lasting as it is not subject to rot, decay, moisture or UV damage, corrosion, or infestation, and it can be reused once crushed.
The trade off is that concrete is heavy and requires more foundations (i.e. more concrete) to support its weight. Concrete also doesn’t tolerate movement, an issue where the ground conditions are poor and a good foundation hard to achieve.
Especially relevant to low energy buildings, concrete and masonry in general absorb heat in hot conditions then release it back into the living space, acting like a whole-house storage radiator. This is often a key design feature of a near zero energy house. And because masonry relies on using small units of construction, you have design flexibility.
However, concrete has a high embodied energy. In other words, it takes a large amount of energy to produce cement. Manufacturers are addressing this challenge by increasing their use of renewable fuels, with the European cement industry aiming for carbon neutrality by 2050, and replacing cement in concrete mixes with waste by products.
Quarrying also has an environmental impact from the point of view of water use, an issue for slate manufacturers too, but the industry has been investing in sustainable extraction methods to mitigate the impact.
Cavity wall construction (blockwork)
The most traditional masonry build technique in Ireland continues to be what’s called a block build, or cavity wall construction.
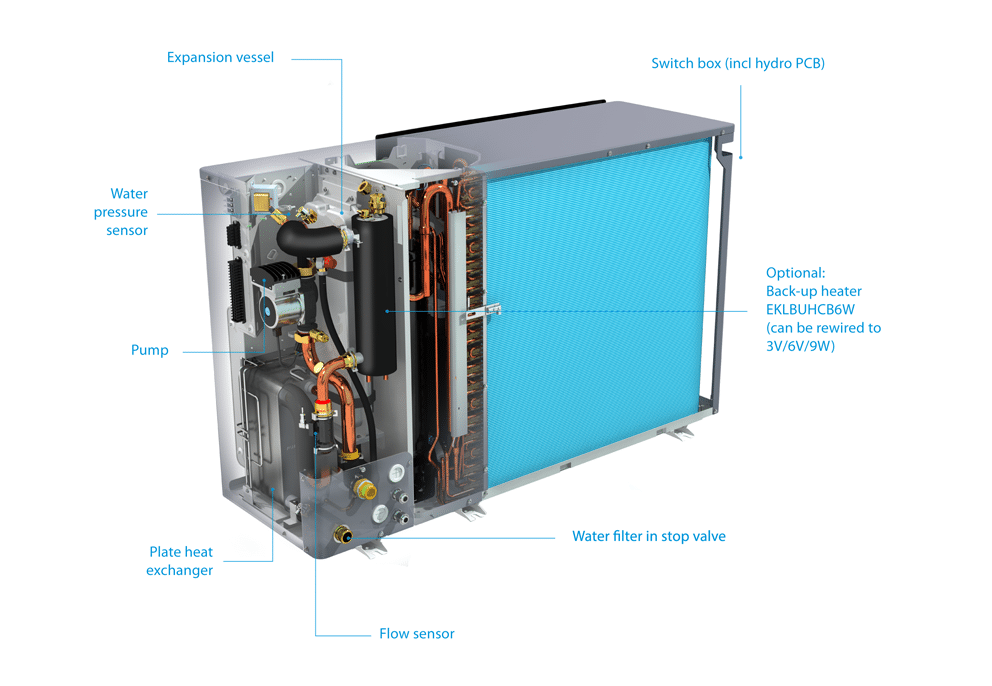
It consists of two rows of blocks or bricks; the inner leaf is often built from regular or lightweight concrete blocks and will usually be built before the outer leaf, although they can be brought up at the same time. Wall ties, added at regular intervals sloping downwards towards the outer leaf, join the two leaves. The blocks are cemented together with mortar.
The inner leaf is the structural component, and thanks to the compressive strength of the concrete blocks, the wall itself becomes the main support for your building.
The cavity between the two layers was originally used to act as a buffer from the elements (to reduce the risk of moisture soaking through) but it is now also used to add insulation, either fully or partially.
Insulating the cavity is specialist work in that the insulation needs to be fully joined at all points and there can be no snots or mortar droppings in the cavity; either of these two scenarios would lead to thermal bridging. If the insulation is not tight against the internal leaf, a phenomenon known as thermal looping will also greatly reduce the insulating effect.
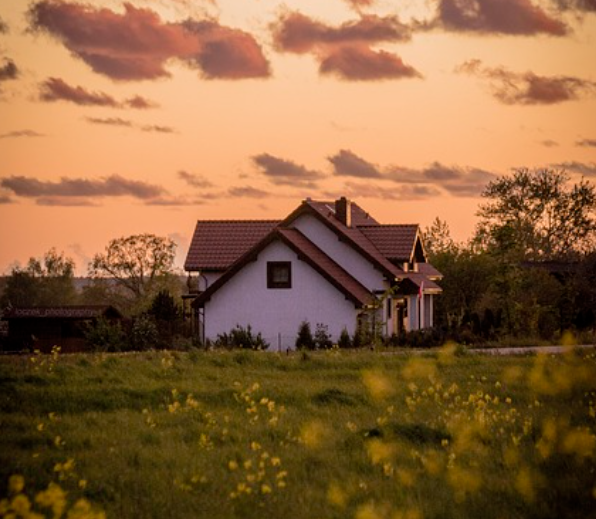
It’s customary to create weep holes at the base of the outer skin to allow water that might penetrate this veneer to escape outside rather than collect in the cavity between. Cavity trays, with associated stop ends and weep holes, must be used above structural openings and above all external wall penetrations.
Though concrete blocks are a relatively recent development from the 1920s, it is only since the 1950s that they completely replaced bricks as the inner leaf of the cavity walling. Bricks are more expensive, and therefore not as readily used because many self-builders nowadays plaster or clad (with stone, for example) their external walls anyway.
The size of the cavity within the blocks has increased over the years to add more insulation; nowadays 150mm cavities are commonplace if you insulate with EPS beads but this can be reduced if you used high spec boards. The size of the cavity will depend on the type of insulation you choose (how good its thermal properties are), whether you full fill or not, and what overall U-value or thermal performance you want to achieve (there is a minimum specified in the building regulations).
Insulation methods
The two most common and cost effective ways to insulate your block build is to either pump the cavity with EPS beads, or install PIR or phenolic rigid boards as the wall is built up. You can also use closed cell spray foam insulation to full fill the cavity, but it’s a more expensive option than the other cavity filling methods.
Insulating externally is also more expensive and therefore not common on new builds, unless it is an intrinsic part of the building method (see Single skin construction below). However for existing buildings it has become a go-to for solid masonry, and some older cavity wall types of construction.
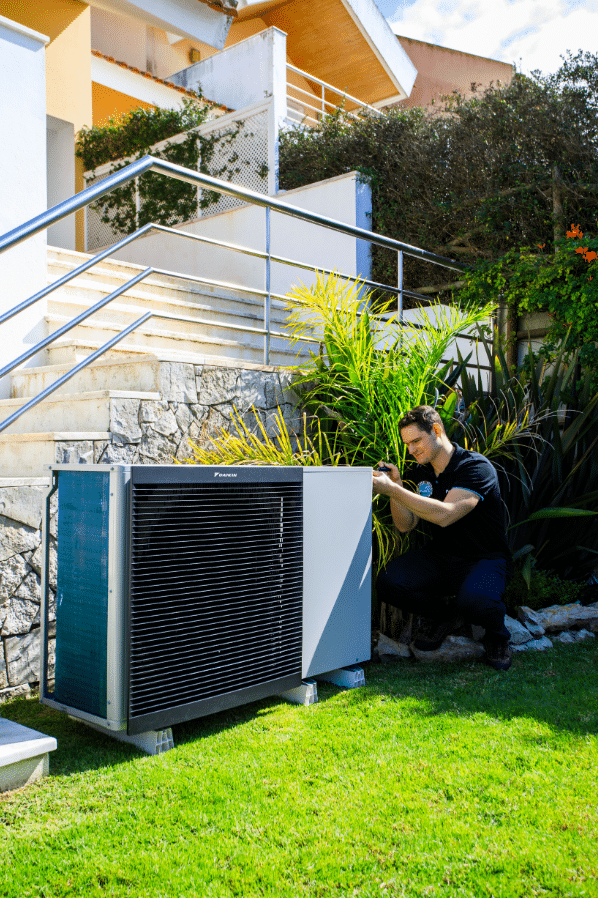
Whether or not you also insulate the internal wall, the one facing inside the house, usually with insulated plasterboard, will depend on your insulation strategy. Structural concrete blocks are therefore usually surfaced with plaster, sand and cement mortar, or covered with (often insulated) plasterboard
to produce the internal wall finish required and add a layer of airtightness. Synthetic fibres incorporated into the sand and cement finish can increase the strength of a block wall considerably.
Your energy assessor will evaluate your options; this is specialist work that takes into account your insulation strategy as a whole – for the entire dwelling, so that there are no weak
links.
Types of blocks
There are three main types of concrete blocks. High density ones made from cement and an aggregate; lower density ones made using cement and industrial wastes/fly ash as the aggregate; and lightweight blocks (including autoclaved aerated blocks) that are easy to lift and use, simple to cut, have good thermal properties and can be made of up to 80 per cent recycled materials.
The standard size of a block is 440mm x 215mm x 100mm but larger sizes are also available, both solid and hollow. It takes ten standard sized concrete blocks to build one square metre of wall. Blocks are usually laid vertically (standing on their long thin edge) but can be laid on flat. This latter method makes for a very strong, solid concrete wall in situations where it’s not possible to cast one from poured concrete.
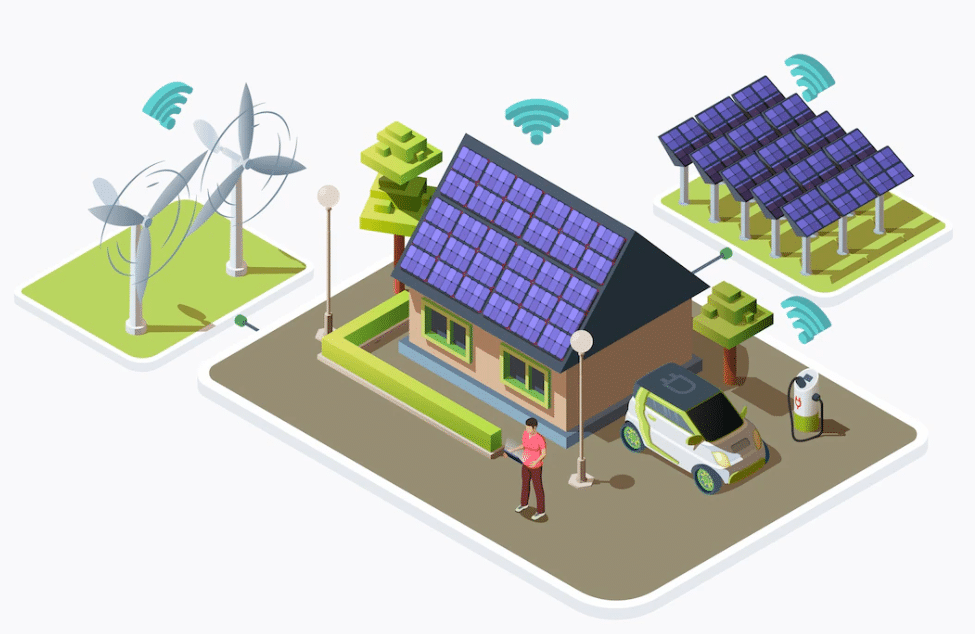
The advantage of concrete blocks is that, being larger they go up faster than bricks. Some blocks, especially concrete types, also absorb less water than brickwork.
Concrete blocks that have a hollow centre can be reinforced, with steel and sections filled with concrete where required, to make the structure very strong. A variant of the concrete block that is gaining popularity is the clay block which is more thermally efficient. This has hollow cavities within it to improve its insulating properties and can be used to build a single skin wall in certain circumstances.
Once on site, blocks have to be carefully stored, out of the wet, on site ready for use; a chipped brick or fractured block is no use to anyone. Weather is another consideration and new work will have to be protected from frost and heavy rain.
Single skin construction and cast concrete
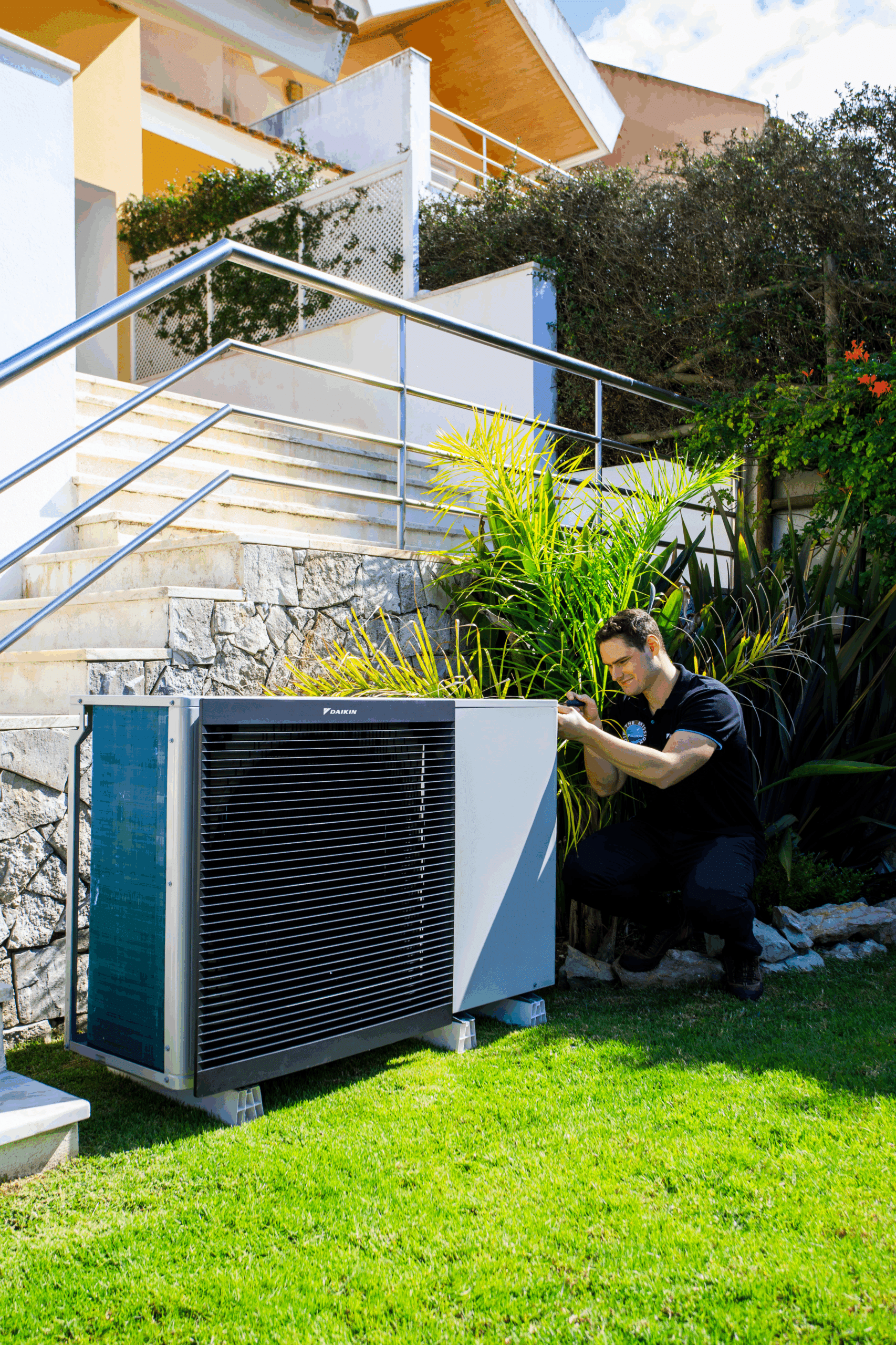
Single skin construction includes prefabricated concrete external wall units, which used to be the sole remit of commercial buildings.
Precast units are quick and easy to install and are brought to site
as needed so there’s no problem with storage. They provide a very good thermal mass but they are also on the more expensive end of the scale and are still rare on self builds. Non load bearing concrete
precast wall units can be used for up to eight storeys or fixed to a steel frame.
An Irish single skin construction system uses 200mm wide blocks that are quickly installed using thin bed mortar, then finished externally with EPS insulation, followed by several other layers to complete the watertight and airtight system. The inside of these lightweight blocks is completed with dot-and-dab plasterboard. It is claimed that this system can cost up to 20 per cent less than timber frame but it is, of course, still a wet trade involving the use of small construction units, just like any other masonry system.
Concrete can also be poured on site to create walls, a prominent example being ICF (see below). Another reason to pour your walls is if you want a specific kind of architectural detail, e.g. by using sandblasted wood boards as your formwork to make an imprint on the concrete. This can be done internally and/or externally.
Of course foundations and floors are also cast in situ, from the subfloor which is made of concrete along with the screed, although the latter can be made of a cement mixture. The mix for a polished concrete floor will have been determined in advance with your supplier. These processes require hiring a cement truck to do the pour on site.
Insulating Concrete Formwork
Insulating Concrete Formwork (ICF) is a wall building method that consists of large, hollow, lightweight polystyrene blocks that lock together to create a mould that is then filled with concrete to make structural walls. It can be used to make roofs too.
The ICF blocks fit snugly together vertically and horizontally and the two leaves are kept in position by various patented metal, plastic or polystyrene spacers. Blocks can be cut on site with a hot wire or a handsaw, but this will be done sparingly as the house will have been designed around the block measurements to minimise waste (in time and materials).
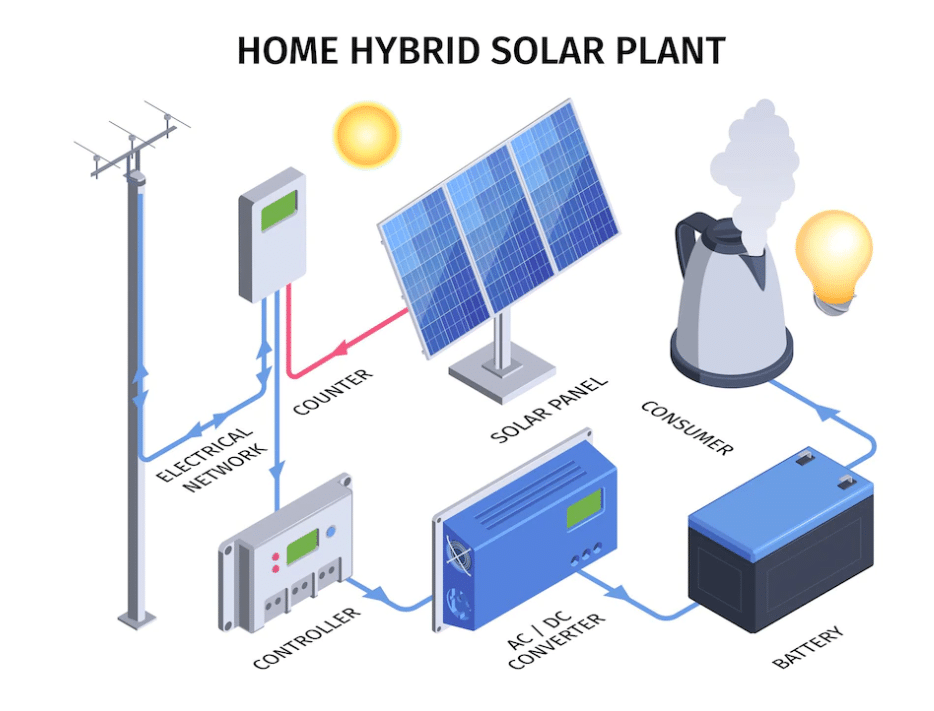
Specialised components such as lintels can be ordered with the package. Many companies have flooring systems that allow you to cast both walls and middle floors at the same time. ICF has all of the benefits of concrete builds, and in addition is intrinsically airtight and virtually thermal bridge-free – a big advantage over other construction methods. U-values can be as good as 0.11W/sqmK but you will have to pay extra to add layers of insulation
It’s quick to erect, can involve DIY help with oversight, is not overly susceptible to bad weather
and offers flexible designs in that curved walls are relatively easy to achieve. As soon as it’s complete, it’s watertight and once it’s roofed, follow-on trades can get cracking much earlier than with other building systems. Manufacturers claim that self-builders can save up to three months on their schedule using this method.
There are several different ICF systems, some of which can cope very well with concrete middle floors, internal walls and all kinds of design requirements. But making changes later (for example adding or moving doors, windows or services) can be difficult and expensive as compared to
blockwork construction which is easy to alter. You’ll find yourself
having to rely on ICF experts with specialist cutting tools and they don’t do this work cheaply.
Without a doubt, the most skilful part of ICF is the pour. Most companies will advise you on this
well before you start your project and at your training days you’ll learn how to support the walls so
they don’t sag or, even worse, burst as you load them with tonnes of wet concrete.
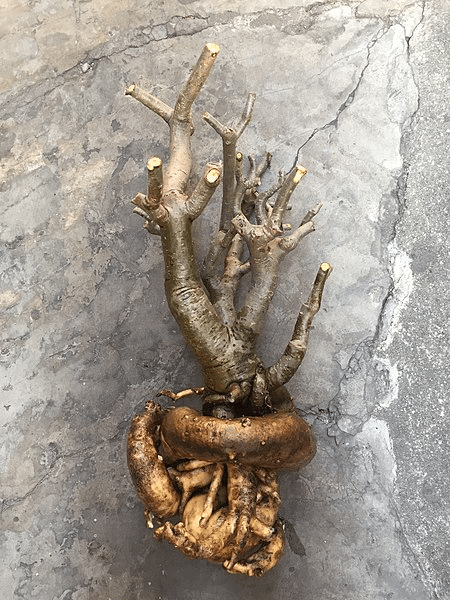
The concrete itself also has to be at exactly the right consistency (wetness) or it won’t flow into all the cavities of the formwork. Some companies insist that you use a particular grade of concrete (aggregate size). Finally, if you are going multi-storey bear in mind that multiple visits of the delivery trucks will cost you.
In terms of finishes, the outer skin of the polystyrene blocks has to be clad (using built-in fixings or wall ties) with something – it can’t be left open to the elements. This outer skin can, though, be easily chased to make room for rainwater downpipes and even other utilities.
In many cases you will need proprietary fixings to finish the external and internal walls, and you can achieve whatever external appearance you want. You could, at this stage, add even more insulation, depending on the U-values you’re aiming to achieve, before your final cladding.
What about flooring?
The most common option nowadays for upper storeys is to use concrete hollowcore or wide slabs, craned into place on site. A concrete upper floor is considered more suited to underfloor heating, as a screed covers the piping, which may mean that you will need to use radiators if your upper floor
is solely made of timber although nowadays timber solutions are also robust. Remember that a concrete floor will be heavy and will require adequate support from the foundations, i.e. more concrete.
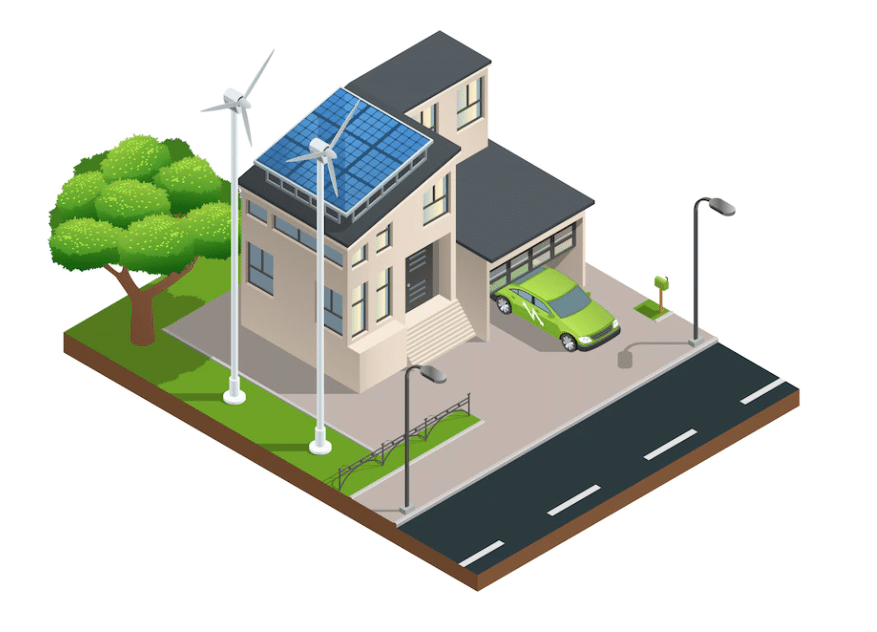
Another option, especially in the case where accessibility is an issue, is the concrete beam and block method whereby concrete blocks are supported on reinforced concrete beams. The joints are grouted and a screed is then applied on top. The strength of the beam and block method allows wider spans of flooring to be constructed without needing extra support.
It is important to research this area prior to construction and select the type of flooring that is most suited to your needs and to select a supplier to consult them on your design. They will be able to advise which method is most cost effective for your requirements, e.g. to support upper floors, requirement for open spans, etc.
The supplier will normally turn around an order very quickly once as-built measurements can be taken on site. Builders may also wish to incorporate balconies and stairs when ordering precast units which will also be manufactured to exact dimensions.
Waste materials as cement substitutes
The most common substitute for cement in the making of concrete in Ireland is a by product of iron manufacturing called GGBS, an acronym for Ground Granulated Blast Furnace Slag. A replacement rate of up to 70 per cent (so 30 per cent Portland cement in the cement mix that goes on to make concrete) is possible under I.S EN 206-1.
An Australian company, meanwhile, is substituting sawdust and other recycled timber, e.g. from discarded pallets, to its mix of cement to make eco-friendly concrete bricks and panels, among other products.
Mostly still at the development stage is Ferrock, which uses steel dust and fly ash to make a cement alternative, capturing CO2 during the curing process. The availability of the waste materials is a barrier to further development. The patent is held by the University of Arizona.