From materials to insulation, your wall construction method impacts cost. Here’s what to consider.
In this article we cover:
- How cavity dimensions affect costs
- Floor-to-ceiling height cost differences
- Wall finish cost differences
- How walls are built up
- U-value requirements and insulation options
When we talk about external walls in terms of cost, we mean the main structure of the property’s outer envelope. This is usually the key structural component and also what gives the house much of its character, alongside the roof.
The external wall starts at the internal ground floor level (DPC level, where the substructure ends) and extends to the wall plate level of the roof.
The cost of external walls comes down to three main factors:
[adrotate banner="58"]- Height – Costs rise with the number of floors and floor-to-ceiling height.
- Makeup – The type of materials and insulation used impact the price.
- Finish – Whether you choose plaster, brick, stone or another finish will affect the final cost.
Common wall construction methods
The most popular method for external wall construction is traditional cavity wall construction, but timber frame is becoming more common. Insulating Concrete Formwork (ICF) is also gaining traction in the UK.
For cavity walls, the typical setup includes:
- An outer leaf
- A cavity with at least 125mm of insulation
- An inner leaf
- A drylining or insulated plasterboard finish
The thickness of the internal insulated plasterboard depends on the required U-value, and costs rise by roughly 10-12% for every extra 10mm of insulation.
The inner leaf of blockwork will usually be 100mm wide unless it needs to support a precast floor slab, in which case it will be 215mm. This change alone will double the quantity of blocks in the inner leaf of a cavity wall. A wider wall means more materials —100mm walls have 9.88 blocks per sqm, while 215mm walls require 20.22 blocks per sqm.
Cavity insulation can be board or pumped-in beads, typically ranging from 100-150mm in thickness. The brand and thickness of insulation will vary in costs, generally rising by around 10% for every extra 10mm added. Block material options include standard concrete, insulative concrete and even insulative clay, each with different price points.
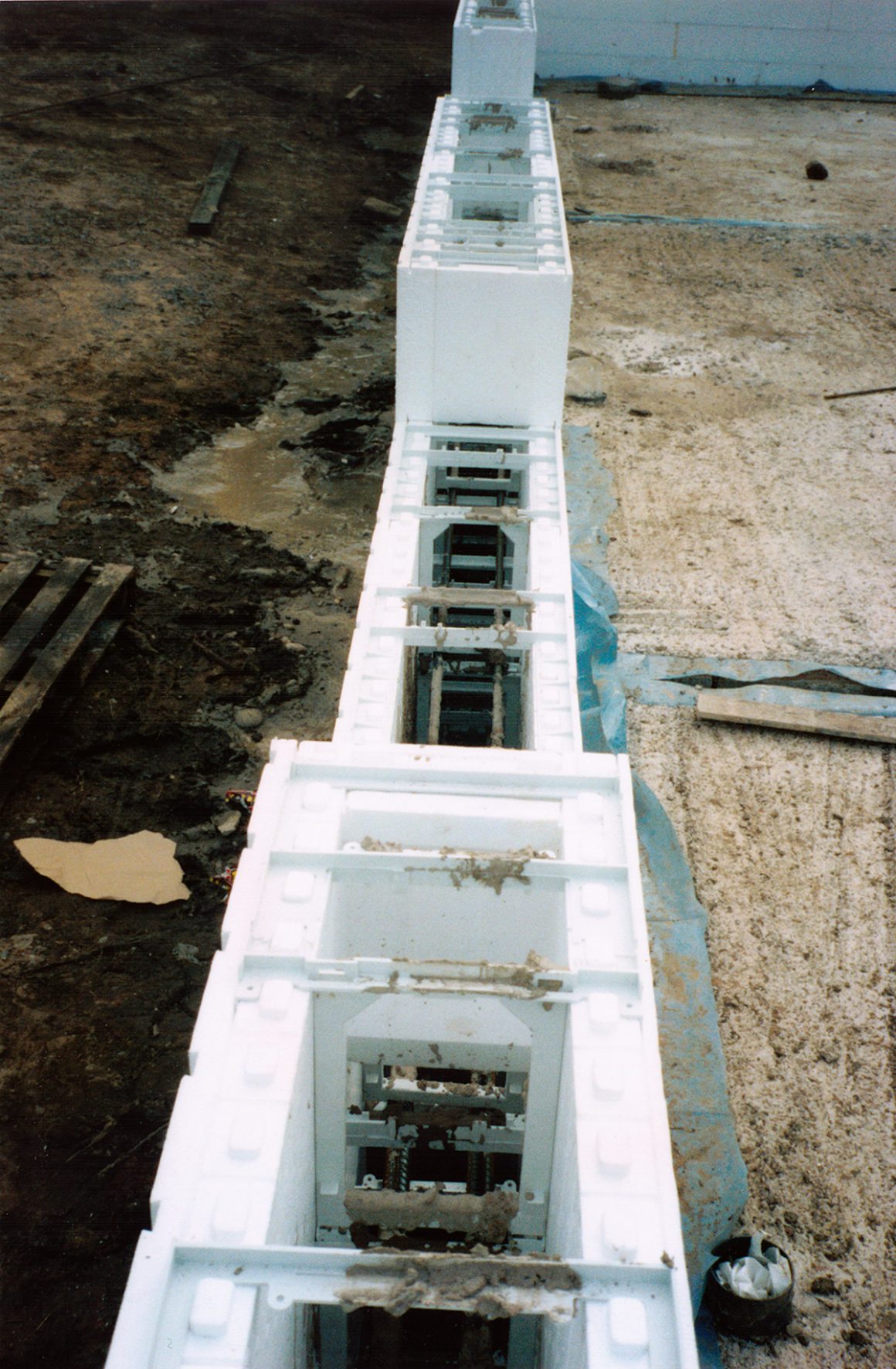
Timber frame and SIPs construction
With timber frame construction, the inner leaf is a prefabricated timber frame designed by a manufacturer. Costs vary depending on design, timber sizes and U-value requirements. Timber frame companies price their systems as a whole, with insulation already integrated.
Standard timber frame options allow for different insulation choices, while Structural Insulated Panels (SIPs) are made of OSB bonded with insulation boards. In an external wall insulation system, the inner leaf is a single 215mm-wide blockwork wall, which carries the floors and roof, with external insulation added.
Wall finishes and their costs
The outer leaf of a cavity wall is mainly there to protect the structure from the weather rather than bear weight. It can be finished in various ways, the most common being:
• 100mm concrete block (requires an additional finish, like plaster)
• Brickwork (a more expensive option due to the number of bricks required)
• Stone finish (usually applied over a blockwork outer leaf)
For timber frame systems, the outer leaf is installed just like a cavity wall but must be tied to the frame for stability. After erecting the timber frame, scaffolding is installed, and the selected outer finish — blockwork, brick or a cement board with a plastered finish — is applied. If cladding is planned, the cement board option is common.
With external wall insulation, the insulation system itself acts as the outer layer. Prices vary widely by manufacturer, so it’s worth shopping around.

Other cost components
Block layers typically charge for work as if no openings exist. They measure the building without deducting windows or doors.
Material selection directly impacts project costs. While concrete was once standard for sills, imported granite and stone are now common but more expensive.
Insulated products are growing in popularity due to airtightness and thermal bridging concerns. They are also lighter and easier to handle, improving safety. This is an extra cost, however.